Tool wear monitoring system capable of realizing self-learning in numerical control machining state
A tool wear and processing state technology, applied in the field of tool wear measurement of CNC machine tools, can solve the problems of affecting the normal processing of the machine tool, changing the structure of the machine tool, and inconvenient operation, so as to achieve real-time monitoring of tool wear status, improve the application range, and facilitate communication.
- Summary
- Abstract
- Description
- Claims
- Application Information
AI Technical Summary
Problems solved by technology
Method used
Image
Examples
Embodiment Construction
[0016] The monitoring system provided by the present invention obtains the machine tool drive motor current signal and the machine tool tool processing information obtained from the numerical control system, goes through a series of signal processing and feature extraction selection processes, and finally monitors the tool wear amount to realize the monitoring of tool wear. Monitor VB, and feed back the monitoring results to the CNC system, and the CNC system responds accordingly according to the wear of the tool, prompting to change the tool or change the tool compensation amount.
[0017] like figure 1 As shown, the monitoring system includes data acquisition and judgment module 1, data processing module 2, feature extraction and selection module 3, fitting prediction trend curve module 4, tool wear rule module 5, tool wear compensation and tool change module 6, tool wear Learning module 7 and tool wear law learning library 8.
[0018] The tool wear law learning library 8 i...
PUM
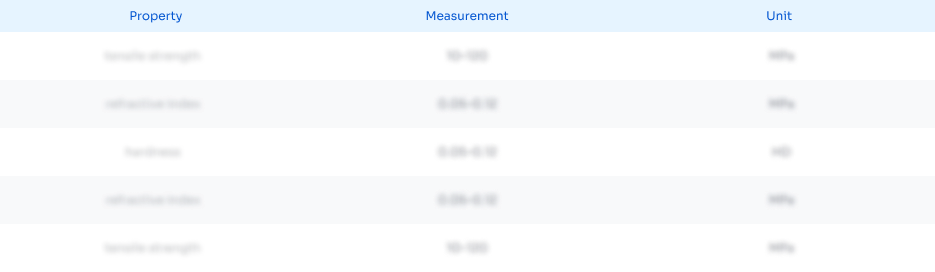
Abstract
Description
Claims
Application Information

- Generate Ideas
- Intellectual Property
- Life Sciences
- Materials
- Tech Scout
- Unparalleled Data Quality
- Higher Quality Content
- 60% Fewer Hallucinations
Browse by: Latest US Patents, China's latest patents, Technical Efficacy Thesaurus, Application Domain, Technology Topic, Popular Technical Reports.
© 2025 PatSnap. All rights reserved.Legal|Privacy policy|Modern Slavery Act Transparency Statement|Sitemap|About US| Contact US: help@patsnap.com