Phase change energy storage thermoplastic composite material and preparation method thereof
A composite material and phase change energy storage technology, which is applied in the field of thermoplastic elastomers, can solve the problems of whether the capsule can remain intact without further research, cannot flow, waste water resources, etc., and achieve good shape retention and elongation at break High, leakage rate reduction effect
- Summary
- Abstract
- Description
- Claims
- Application Information
AI Technical Summary
Benefits of technology
Problems solved by technology
Method used
Examples
Embodiment 1
[0046] Mix polypropylene 25%, EPDM rubber 43%, SP2045 crosslinking agent 5%, 58# paraffin 25%, antioxidant (1010) 0.2%, zinc oxide 1.3%, stearic acid 0.5% by weight Uniform, one-step dynamic vulcanization in twin-screw extrusion to prepare phase-change energy-storage thermoplastic composites. The temperature setting of the heating zone of the twin-screw extruder is: 160°C, 170°C, 180°C, 180°C, 180°C, 180°C, 180°C, 180°C, 180°C (the order is from the feed port to the machine head) , speed 500rpm.
Embodiment 2
[0048] Propylene 18%, EPDM rubber 25%, 58# paraffin 50%, 1790 antioxidant 0.1%, 168 antioxidant 0.1%, zinc oxide 1.3%, stearic acid 0.5%, cross-linking assistant agent (SnCl 2 ) 2% were mixed evenly, and the premix A was prepared by melting and kneading with an internal mixer at a temperature of 180-200° C. and a rotation speed of 30 rpm.
[0049] Mix the above premix A with 3% phenolic resin SP1045 evenly, and use twin-screw extrusion for dynamic vulcanization to prepare phase-change energy storage thermoplastic composite materials. The temperature in the heating zone of the twin-screw extruder is set at: 160°C, °C, 180°C, 180°C, 180°C, 180°C, 180°C, 180°C, 180°C (the order is from the feeding port to the machine head), the speed is 500rpm.
Embodiment 3
[0051] According to the weight, mix 5 kg of polypropylene, 13.8 kg of EPDM rubber, 70 kg of 58# paraffin, 0.2 kg of antioxidant (1790), 0.8 kg of zinc oxide, and 0.2 kg of stearic acid. Melt kneading at 200°C to prepare reaction one-step material B1.
[0052] Mix 2 kg of EPDM rubber with cross-linking aid (SnCl 2 ) 2 kg was mixed evenly, and the accelerator masterbatch B2 was prepared by melting and mixing equipment.
[0053] Mix 3 kg of EPDM rubber and 3 kg of SP1045 cross-linking agent evenly, and prepare cross-linking agent masterbatch B3 by using melt mixing equipment.
[0054] Mix 90% of the reaction one-step material B1, 4% of the accelerator masterbatch B2 and 6% of the crosslinker masterbatch B3 in a weight ratio, and use twin-screw extrusion for dynamic vulcanization to prepare a phase-change energy storage thermoplastic composite material, The temperature setting of the heating zone of the twin-screw extruder is: 160°C, 170°C, 180°C, 180°C, 180°C, 180°C, 180°C, 18...
PUM
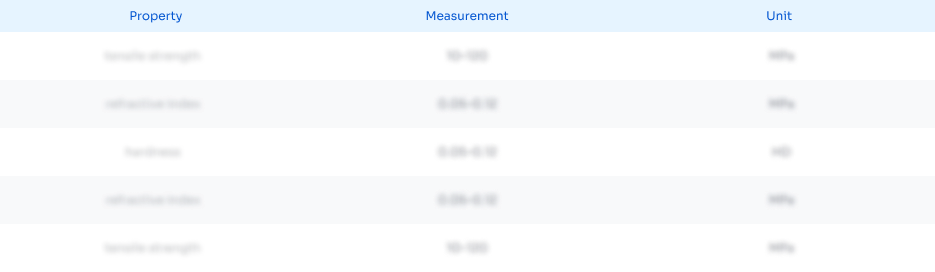
Abstract
Description
Claims
Application Information

- R&D
- Intellectual Property
- Life Sciences
- Materials
- Tech Scout
- Unparalleled Data Quality
- Higher Quality Content
- 60% Fewer Hallucinations
Browse by: Latest US Patents, China's latest patents, Technical Efficacy Thesaurus, Application Domain, Technology Topic, Popular Technical Reports.
© 2025 PatSnap. All rights reserved.Legal|Privacy policy|Modern Slavery Act Transparency Statement|Sitemap|About US| Contact US: help@patsnap.com