Method for preparing 2-mercaptobenzothiazole
A technology of mercaptobenzothiazole and aniline, which is applied in the field of rubber vulcanization accelerator production, can solve the problem of low yield and achieve the effect of reducing the generation of asphalt-like waste
- Summary
- Abstract
- Description
- Claims
- Application Information
AI Technical Summary
Problems solved by technology
Method used
Image
Examples
Embodiment 1
[0031](1) in the reactor of 1.2L, add 400g aniline, 344g sulfur and 360g carbon disulfide are totally 1106g, (reactant proportioning is aniline: sulfur: carbon disulfide is 1: 2.5: 1.1) at 250~260 ℃, react 90min, this When the reaction is 9.1MPa, the reaction is terminated to obtain a crude product melt. Using the self-pressure generated by the reaction, the crude MBT melt is pressed into a 3L crystallizer equipped with 1200g of carbon disulfide at 140°C. The maximum temperature of the mixed solution after mixing is 165 °C. ℃, lower the temperature at a cooling rate of 0.5℃ / min, start to discharge hydrogen sulfide when the temperature in the crystallizer is 90℃, control the discharge time of hydrogen sulfide to 30min, the temperature of the mixture drops to 18℃, filter to obtain MBT filter cake and carbon disulfide mother liquor, use 600g The filter cake was washed twice with carbon disulfide, and dried under vacuum at room temperature to obtain 542 g of MBT product with a puri...
Embodiment 2
[0039] (1) in the reactor of 0.6L, add 212g aniline, 117g sulfur and 260g carbon disulfide total 589g, (reactant proportioning is aniline: sulfur: carbon disulfide is 1: 1.6: 1.5) react 120min at 240~250 ℃, stop reaction, and the reaction pressure was 6.9 MPa at this time. Using the self pressure generated by the reaction, the crude MBT melt was pressed into a 2L crystallizer containing 1000g of carbon disulfide at 130°C. The maximum temperature of the mixed liquid after mixing was 153.5°C, and the temperature was lowered at a cooling rate of 0.5°C to 1°C / min. When the temperature of the mixture in the crystallizer dropped to 70°C, hydrogen sulfide began to be discharged, the time for discharging hydrogen sulfide was controlled at 30 minutes, the temperature of the mixture was lowered to 20°C, and the MBT filter cake and carbon disulfide mother liquor were obtained by filtration, and the filter cake was washed twice with 500 g of carbon disulfide. It was dried under vacuum to ...
PUM
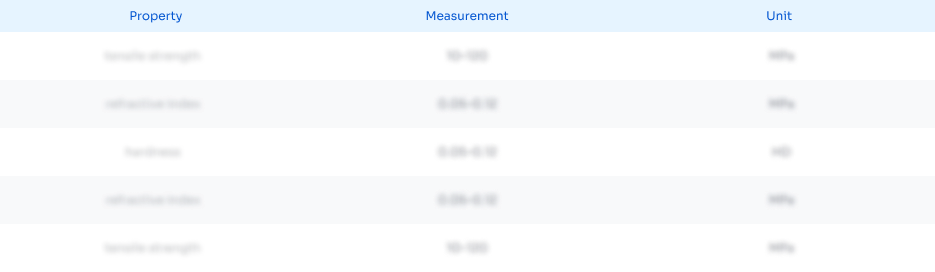
Abstract
Description
Claims
Application Information

- R&D
- Intellectual Property
- Life Sciences
- Materials
- Tech Scout
- Unparalleled Data Quality
- Higher Quality Content
- 60% Fewer Hallucinations
Browse by: Latest US Patents, China's latest patents, Technical Efficacy Thesaurus, Application Domain, Technology Topic, Popular Technical Reports.
© 2025 PatSnap. All rights reserved.Legal|Privacy policy|Modern Slavery Act Transparency Statement|Sitemap|About US| Contact US: help@patsnap.com