Method for preparing high-purity manganese sulfate and high-purity manganese carbonate by reduction leaching of pyrolusite through scrap iron
A technology of pyrolusite and manganese sulfate, applied in manganese sulfate, chemical instruments and methods, ferric sulfate, etc., can solve the problems of large impurity content, high production cost, complicated process, etc., and achieves reduction of impurity ions, easy operation, and technological process simple effect
- Summary
- Abstract
- Description
- Claims
- Application Information
AI Technical Summary
Problems solved by technology
Method used
Image
Examples
Embodiment 1
[0028] Add pyrolusite and deionized water to the reaction kettle, slowly add 98% concentrated sulfuric acid under mechanical stirring, so that the liquid-solid mass ratio in the reaction kettle is 8:1, after mixing evenly, the temperature rises to 50°C and then adds iron Shavings, the initial concentration of sulfuric acid in the reactor is 1.0mol / L, the molar ratios of iron filings, sulfuric acid and manganese dioxide in pyrolusite are 0.6:1 and 2:1 respectively, and after 0.5h of reaction, the temperature is raised to 100°C to continue the reaction for 1h , under the constant condition of keeping the temperature in the reactor, add calcium carbonate to adjust the pH value of the solution to 5 so that the ferric iron in the solution is completely hydrolyzed to ferric hydroxide, obtain the filter residue and the initial filtrate of manganese sulfate through filtration, and add to the obtained sulfuric acid Barium sulfide was added to the primary manganese filtrate to make the N...
Embodiment 2
[0030] Add pyrolusite and deionized water to the reaction kettle, slowly add 98% concentrated sulfuric acid under mechanical stirring, so that the liquid-solid mass ratio in the reaction kettle is 5:1, after mixing evenly, the temperature rises to 30°C and iron filings are added , the initial concentration of sulfuric acid in the reactor is 1.5mol / L, and the mol ratios of iron filings, sulfuric acid and manganese dioxide in pyrolusite are respectively 1.3:1, 1.5:1, and the reaction is heated up to 80°C for 1h to continue the reaction for 0.5h. Under the condition of keeping the temperature in the reaction kettle constant, add calcium carbonate to adjust the pH value of the solution to 6 so that the ferric iron in the solution is completely hydrolyzed into ferric hydroxide, and the initial filtrate of manganese sulfate is obtained by filtration, and the obtained manganese sulfate initial Add sodium dimethyl dithiocarbamate (SDD) in the filtrate to make the Ni in the solution 2+...
Embodiment 3
[0032] Add pyrolusite and deionized water to the reaction kettle, slowly add 98% concentrated sulfuric acid under mechanical stirring, so that the liquid-solid mass ratio in the reaction kettle is 10:1, mix evenly and raise the temperature to 60°C and add iron filings , the initial concentration of sulfuric acid in the reactor was 2.0mol / L, and the molar ratios of iron filings, sulfuric acid and manganese dioxide in pyrolusite were 1.0:1 and 2.5:1 respectively. After 1 hour of reaction, the temperature was raised to 70°C to continue the reaction for 1.5 hours. Under the constant temperature condition in the reactor, add calcium carbonate to adjust the pH value of the solution to 5.5 and make the ferric iron in the solution be completely hydrolyzed to ferric hydroxide, obtain the first filtrate of manganese sulfate through filtration, and add the first filtrate to the manganese sulfate first filtrate of gained A mixture of barium sulfide and sodium dimethyldithiocarbamate (SDD) ...
PUM
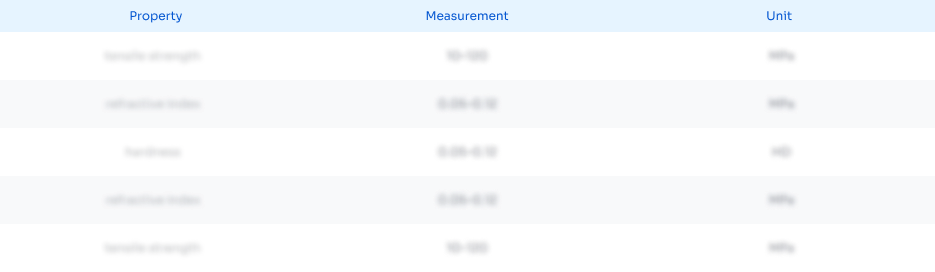
Abstract
Description
Claims
Application Information

- R&D
- Intellectual Property
- Life Sciences
- Materials
- Tech Scout
- Unparalleled Data Quality
- Higher Quality Content
- 60% Fewer Hallucinations
Browse by: Latest US Patents, China's latest patents, Technical Efficacy Thesaurus, Application Domain, Technology Topic, Popular Technical Reports.
© 2025 PatSnap. All rights reserved.Legal|Privacy policy|Modern Slavery Act Transparency Statement|Sitemap|About US| Contact US: help@patsnap.com