Method for determining rigidity of bolt connecting piece
A determination method and technology for connecting parts, which are applied in special data processing applications, instruments, electrical and digital data processing, etc., can solve the problems that the macro-scale of bolted connections is difficult to achieve, and the influence of bolt stiffness is not involved.
- Summary
- Abstract
- Description
- Claims
- Application Information
AI Technical Summary
Problems solved by technology
Method used
Image
Examples
example 1
[0051] 1. The calculation of the stiffness of the bolted joint in Example 1 includes the following steps:
[0052] 1) According to the actual size of the bolted joint and the actual appearance of the joint surface, the macro-micro finite element simulation model of the bolted joint is established in a layer-by-layer manner from the macroscopic size to the microscopic appearance;
[0053] 2) According to the macro-micro finite element model of the bolted joint, the stiffness model of the bolted joint is established, and the stiffness of the bolted joint is divided into two parts: the matrix stiffness of the bolted joint and the stiffness of the joint surface of the bolted joint. The stiffness of these two parts is obtained through series connection The stiffness of the entire bolted joint, where the stiffness of the joint surface of the bolted joint is obtained by connecting the stiffnesses of each contact asperity in parallel;
[0054] 3) The application and simulation calcula...
example 2
[0080] Establish the same test piece as Example 1, the difference is that Example 2 is only tightened once, and the tightening process is 0:1.5s to directly reach the pre-tightening force of 9000N. The specific implementation steps are the same as the example 1, except that the loading of the bolt force is different from the example 1. As mentioned above, the calculation is performed after the finite element model is established. According to the simulation calculation results and the established connector stiffness model, the stiffness of the bolted connector is calculated, which specifically includes the following steps:
[0081] 1) Calculate the stiffness of the first-level model
[0082] Same as the method of Example 1, the judging condition judges the range of the pressure distribution. The coordinate value of the zero point is 14.517mm, and the contact half angle α=34.55°, so the stiffness of the first-level model is:
[0083]
[0084] 2) Calculate the stiffness of ...
PUM
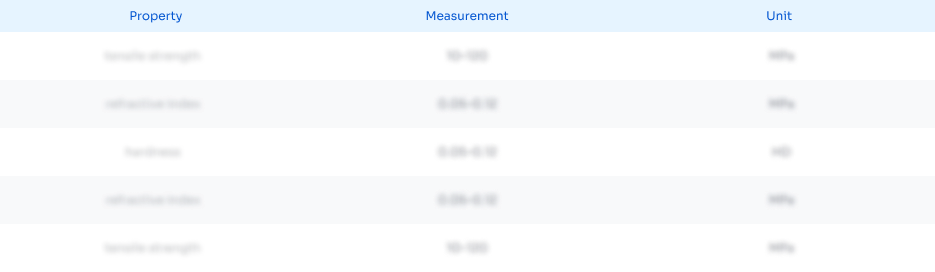
Abstract
Description
Claims
Application Information

- R&D
- Intellectual Property
- Life Sciences
- Materials
- Tech Scout
- Unparalleled Data Quality
- Higher Quality Content
- 60% Fewer Hallucinations
Browse by: Latest US Patents, China's latest patents, Technical Efficacy Thesaurus, Application Domain, Technology Topic, Popular Technical Reports.
© 2025 PatSnap. All rights reserved.Legal|Privacy policy|Modern Slavery Act Transparency Statement|Sitemap|About US| Contact US: help@patsnap.com