Preparation method of trimethylolpropane diallyl ether
A technology of trimethylolpropane diallyl ether and methylolpropane diallyl ether, which is applied in the field of preparation of trimethylolpropane diallyl ether, can solve problems that are not conducive to industrial production and increase side effects. Reaction, large equipment investment and other issues, to achieve stable and reliable product quality, reduced reaction side reactions, and stable chemical properties
- Summary
- Abstract
- Description
- Claims
- Application Information
AI Technical Summary
Problems solved by technology
Method used
Examples
Embodiment 1
[0020] Add 1mol (135.5g) of trimethylolpropane, 2mol (83.3g) of sodium hydroxide, and 220ml of solvent butyl ether into a 1000ml four-necked bottle, install stirring, a thermometer and an oil-water separator, and gradually heat up with an electric heating mantle. When the temperature reaches At 93°C, the butyl ether-water component evaporates, and when the temperature rises to about 105°C, almost no water comes out, and the dehydration time is about 1.5-2h. Stop the dehydration, then lower the temperature to 65°C and start to add 2.05mol (158.5g) of allyl chloride dropwise, the dropwise addition time is about 1.5-2.0h, and control the reaction temperature at 65-70°C, continue to stir the reaction for 3.0h after the dropwise addition To ensure the completion of the etherification reaction, add 300ml of water after the reaction, stir until the generated salt is completely dissolved, then add 2g of sodium sulfite, and at the same time adjust the pH to neutral with 15% hydrochloric...
Embodiment 2
[0022] Add 1mol (135.5g) of trimethylolpropane, 2.1mol (84g) of sodium hydroxide, and 220ml of solvent butyl ether into a 1000ml four-necked bottle, install stirring, a thermometer and an oil-water separator, and gradually heat up to 93°C with an electric heating mantle. Azeotropic dehydration until no water in the fraction is analyzed, then drop the temperature to 65°C and start adding 2.1mol (162.3g) of chloropropene dropwise for about 3 hours. After the dropwise addition, continue to stir for 1.0h to ensure the etherification reaction After the completion of the reaction, add 300ml of water, stir until the generated salt is completely dissolved, then add 3g of sodium sulfite, and at the same time adjust the pH to neutral with 15% hydrochloric acid, pour it into a separatory funnel and let it stand for about 20-30min, then separate the lower layer Brine, the upper organic phase was distilled under normal pressure to recover the butyl ether solvent, and then rectified under re...
Embodiment 3
[0024] Add 5mol (677.5g) of trimethylolpropane, 380g (1.9mol) of sodium hydroxide, and 1,000ml of solvent butyl ether into a 5000ml four-necked bottle, install stirring, a thermometer and an oil-water separator, and gradually heat up to 93°C with an electric heating mantle. Azeotropic dehydration until the water does not come out, then lower the temperature to 65°C and start to add 11mol (850g) of allyl chloride dropwise for about 2 hours. After the dropwise addition, continue to stir and react for 2.0 hours to ensure the completion of the etherification reaction. Add 1200ml of water, stir until the generated salt is completely dissolved, then add 10g of sodium sulfite, and adjust the pH to neutral with 15% hydrochloric acid at the same time, pour it into a separatory funnel and let it stand for about 20-30min, then separate the lower layer of brine, and the upper layer of organic phase. The butyl ether solvent was recovered by pressure distillation, followed by rectification u...
PUM
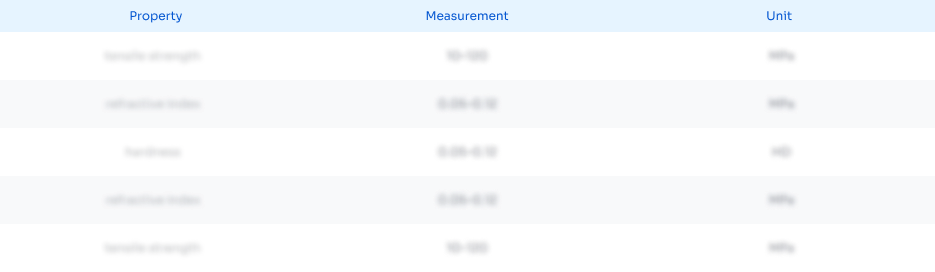
Abstract
Description
Claims
Application Information

- R&D
- Intellectual Property
- Life Sciences
- Materials
- Tech Scout
- Unparalleled Data Quality
- Higher Quality Content
- 60% Fewer Hallucinations
Browse by: Latest US Patents, China's latest patents, Technical Efficacy Thesaurus, Application Domain, Technology Topic, Popular Technical Reports.
© 2025 PatSnap. All rights reserved.Legal|Privacy policy|Modern Slavery Act Transparency Statement|Sitemap|About US| Contact US: help@patsnap.com