Damping coupling
A technology of couplings and damping springs, applied in the direction of couplings, elastic couplings, mechanical equipment, etc., can solve the problem that rigid couplings cannot absorb the vibration and shock of motors and transmissions, and reduce the reliability of motors and transmission system components Sex and life, the reliability of ordinary elastic couplings, and the axial and radial dimensions cannot be directly selected to achieve the effects of avoiding vibration damping compression deformation, superior performance, and stable damping
- Summary
- Abstract
- Description
- Claims
- Application Information
AI Technical Summary
Problems solved by technology
Method used
Image
Examples
Embodiment Construction
[0017] Below in conjunction with accompanying drawing and embodiment the present invention will be further described:
[0018] Such as figure 1 , 2 A vibration-damping coupling shown is composed of a flange 1 , a driven plate 2 , a hub 3 , a vibration-damping disk 4 and a vibration-damping spring 5 . The flange plate 1, the driven plate 2, the disc hub 3 and the damping plate 4 are all disc structures and coaxially installed. The inner hole of the flange 1 is a flat key hole, and the flange 1 is set on the motor output shaft 12 through the flat key 13; the right end of the flange 1 extends outward to form an opening 1a, and the outer edge of the opening 1a has a The outer flange 1b perpendicular to the axis of the disc 1 is connected to the driven piece 2 by first rivets 9, and the first rivets 9 are evenly distributed on the circumference. The hub 3 is composed of a hub web 3a and a hub core 3b. The inner hole of the hub core 3b is a spline hole. The hub core 3b is set on ...
PUM
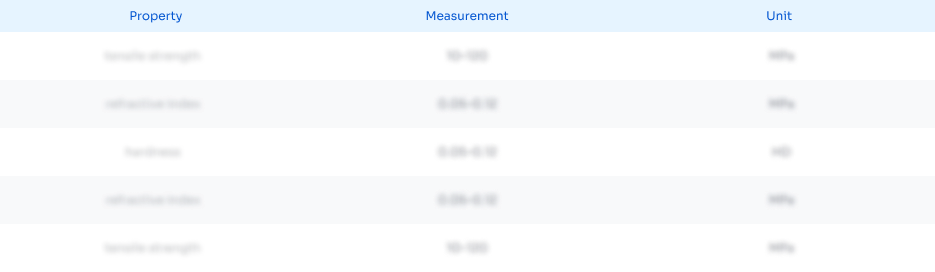
Abstract
Description
Claims
Application Information

- R&D
- Intellectual Property
- Life Sciences
- Materials
- Tech Scout
- Unparalleled Data Quality
- Higher Quality Content
- 60% Fewer Hallucinations
Browse by: Latest US Patents, China's latest patents, Technical Efficacy Thesaurus, Application Domain, Technology Topic, Popular Technical Reports.
© 2025 PatSnap. All rights reserved.Legal|Privacy policy|Modern Slavery Act Transparency Statement|Sitemap|About US| Contact US: help@patsnap.com