Large asynchronous motor rotor fanning strip lamination structure
A technology for asynchronous motors and segments, which is applied in the direction of magnetic circuit shape/style/structure, manufacturing stator/rotor body, magnetic circuit rotating parts, etc., and can solve the problems of lamination failure, screw bending, low efficiency of rotor segment assembly, etc. problems, to achieve the effect of improving reliability, simple structure, and reducing the difficulty of lamination
- Summary
- Abstract
- Description
- Claims
- Application Information
AI Technical Summary
Problems solved by technology
Method used
Image
Examples
Embodiment Construction
[0013] The specific embodiments of the present invention will be further described below in conjunction with the accompanying drawings.
[0014] Such as figure 1 As shown, the present invention includes a rotor segment 1, a screw rod 2, a hex nut 3, a rotor end plate 4, a pin 5, a rotor ventilation groove plate 6, a rotor pressure ring 7, an oblique key 8 and a rotor bracket 9. The rotor pressure ring 7 is closed on the rotor bracket 9 . The rotor end plate 4 , the rotor ventilation slot plate 6 and the rotor segment 1 are positioned and laminated on the rotor bracket 9 and between the two rotor pressure rings 7 through the pin 5 . The screw rod 2 runs through the laminated rotor end plate 4 , the rotor ventilation slot plate 6 and the rotor sector piece 1 , and the hex nuts 3 are fastened to both ends of the screw rod 2 . The oblique key 8 fastens the structure between the two rotor pressure rings 7 as a whole.
[0015] The stacking process is as follows: first, put a roto...
PUM
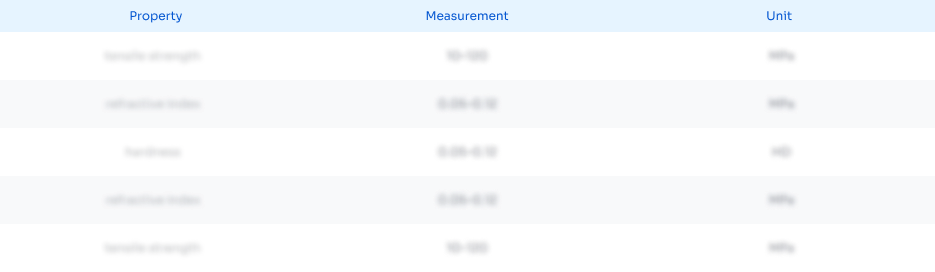
Abstract
Description
Claims
Application Information

- R&D
- Intellectual Property
- Life Sciences
- Materials
- Tech Scout
- Unparalleled Data Quality
- Higher Quality Content
- 60% Fewer Hallucinations
Browse by: Latest US Patents, China's latest patents, Technical Efficacy Thesaurus, Application Domain, Technology Topic, Popular Technical Reports.
© 2025 PatSnap. All rights reserved.Legal|Privacy policy|Modern Slavery Act Transparency Statement|Sitemap|About US| Contact US: help@patsnap.com