Process for synthesizing calcium zirconate by liquid-phase and solid-phase mixed calcination method
A solid-phase calcining method and liquid-phase mixing technology, applied in zirconium compounds, chemical instruments and methods, inorganic chemistry, etc., can solve the problems of high equipment requirements, unrealistic large-scale production, and high cost, and achieve short production process flow and operation. Easy control and high product quality effect
- Summary
- Abstract
- Description
- Claims
- Application Information
AI Technical Summary
Problems solved by technology
Method used
Examples
Embodiment 1
[0009] In the first step, put 20L of purified water into a 50L reactor and start stirring; in the second step, put 10KgZBC (39.5%ZrO 2 ) and 3.25Kg calcium carbonate (55.5%CaO) were put into the reaction kettle and stirred for 30 minutes; the third step was to put the slurry directly into the centrifuge for centrifugal dehydration for 5 minutes; the fourth step was to determine the water content of the material after preliminary dehydration 40%-50%, put it into a quartz crucible, send it into a tunnel kiln, and control the central temperature at 950°C-970°C; step 5, discharge after 16 hours, cool, ball mill for 30 minutes, and pack to get the finished product.
Embodiment 2
[0011] In the first step, put 22L of purified water into a 50L reactor and start stirring; in the second step, 10KgZBC (40.2%ZrO 2 ) and 3.3Kg calcium carbonate (55.5% CaO) were put into the reaction kettle and stirred for 40 min; in the third step, the slurry was directly put into the centrifuge for centrifugal dehydration for 15 min; in the fourth step, the water content of the material after preliminary dehydration was 45 %, put it into a quartz crucible, send it into a tunnel kiln, and control the central temperature at 930°C-960°C; the fifth step is to discharge the material after 17 hours, cool it, and ball mill it for 50 minutes, and then pack it to get the finished product.
Embodiment 3
[0013] In the first step, put 18L of purified water into a 50L reactor and start stirring; in the second step, put 10KgZOH (40.6%ZrO 2 ) and 3.3Kg calcium carbonate (55.8%CaO) were put into the reaction kettle and stirred for 32 min; the third step, the slurry was directly put into the centrifuge for centrifugal dehydration; the fourth step, the water content of the material after preliminary dehydration was 50 %, put it into a quartz crucible, send it into a tunnel kiln, and control the central temperature at 900°C-940°C; the fifth step, discharge after 20h, cool and pack to obtain the finished product.
PUM
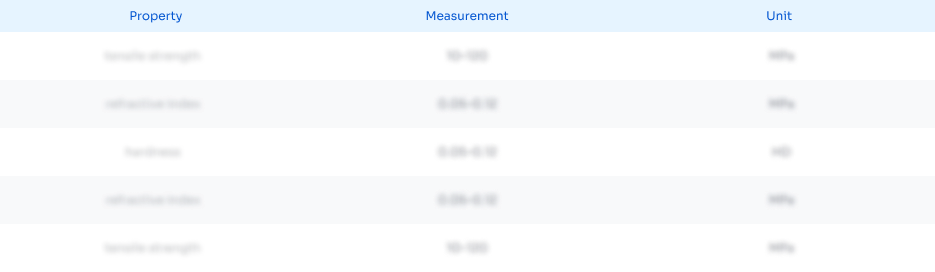
Abstract
Description
Claims
Application Information

- R&D
- Intellectual Property
- Life Sciences
- Materials
- Tech Scout
- Unparalleled Data Quality
- Higher Quality Content
- 60% Fewer Hallucinations
Browse by: Latest US Patents, China's latest patents, Technical Efficacy Thesaurus, Application Domain, Technology Topic, Popular Technical Reports.
© 2025 PatSnap. All rights reserved.Legal|Privacy policy|Modern Slavery Act Transparency Statement|Sitemap|About US| Contact US: help@patsnap.com