Manufacture method of metal composite board
A technology of metal composite panels and manufacturing methods, applied in the direction of metal layered products, chemical instruments and methods, lamination, etc., can solve the problems of low efficiency, low composite strength, and inability to produce composite strength, etc. The effect of less deformation and high yield
- Summary
- Abstract
- Description
- Claims
- Application Information
AI Technical Summary
Problems solved by technology
Method used
Image
Examples
Embodiment Construction
[0015] The present invention will be further described below in conjunction with the accompanying drawings and embodiments.
[0016] see Figure 1 to Figure 4 , a method for manufacturing a metal composite panel, comprising the steps of:
[0017] (1) cleaning the composite surface of the base layer blank 1 and the multilayer blank 2 to remove surface impurities;
[0018] (2) On the composite surface of the base blank 1, the concave-convex lines 3 or the concave-convex blocks 4 are pressed with a mold, and the concave-convex lines 3 on the composite surface of the base blank 1 are also made with a mold on the composite surface of the base blank 1 Or concave-convex block 4 matching concave-convex line 3 or concave-convex block 4. As a preference, the composite surface of this embodiment is preferably made with concave-convex lines 3 , and the mold can be a concave-convex mold capable of producing concave-convex lines 3 .
[0019] (3) The base layer blank 1 and the multi-layer...
PUM
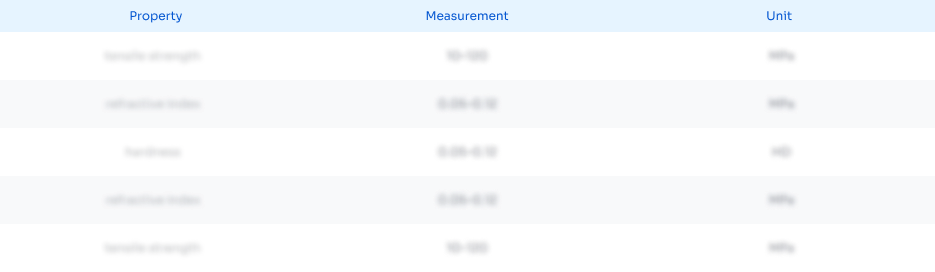
Abstract
Description
Claims
Application Information

- Generate Ideas
- Intellectual Property
- Life Sciences
- Materials
- Tech Scout
- Unparalleled Data Quality
- Higher Quality Content
- 60% Fewer Hallucinations
Browse by: Latest US Patents, China's latest patents, Technical Efficacy Thesaurus, Application Domain, Technology Topic, Popular Technical Reports.
© 2025 PatSnap. All rights reserved.Legal|Privacy policy|Modern Slavery Act Transparency Statement|Sitemap|About US| Contact US: help@patsnap.com