Machining method of traveling thrust wheel of large excavator
A processing method and technology of supporting rollers, which are applied in the field of mechanical processing, can solve the problems that the mechanical performance and serviceability of supporting rollers cannot meet the production and use, and achieve the effects of easy control of casting size, low production cost, and shortened production cycle
- Summary
- Abstract
- Description
- Claims
- Application Information
AI Technical Summary
Problems solved by technology
Method used
Image
Examples
Embodiment 1
[0018] Embodiment 1: as figure 2 As shown, a processing method of a large excavator walking track roller, first adopts silicon-manganese steel to cast a track roller blank, and then through mechanical finishing into a finished track roller; and figure 1 Compared with the processing of original forgings, the machining allowance of the supporting wheel is greatly reduced, saving raw materials and reducing the workload of machining. In the figure, 1 is the processing allowance part of the supporting wheel, and 2 is the finished section of the supporting wheel. Higher strength grade materials are used to replace the original supporting wheel materials, and the mechanical properties and service performance are not lower than the original forging material level. The silicon-manganese steel used is made of the following components: carbon 0.18%, silicon 1.5%, manganese 1.5%. , 0.5% chromium, 0.01% sulfur, 0.01% phosphorus, and the balance is iron and unavoidable impurities, express...
Embodiment 2~5
[0023] Embodiment 2~5: a kind of processing method of large-scale excavator traveling roller, its preparation method is the same as embodiment 1, and difference is that the content of the component of silicon-manganese steel used is different, and the content of each component is shown in Table 2 .
[0024] The content of each component in table 2 embodiment 2~5, by weight percentage;
[0025] Example
[0026] The balance is iron and unavoidable impurities.
PUM
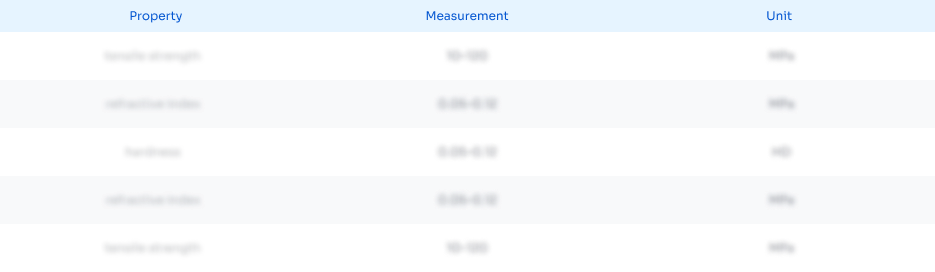
Abstract
Description
Claims
Application Information

- R&D
- Intellectual Property
- Life Sciences
- Materials
- Tech Scout
- Unparalleled Data Quality
- Higher Quality Content
- 60% Fewer Hallucinations
Browse by: Latest US Patents, China's latest patents, Technical Efficacy Thesaurus, Application Domain, Technology Topic, Popular Technical Reports.
© 2025 PatSnap. All rights reserved.Legal|Privacy policy|Modern Slavery Act Transparency Statement|Sitemap|About US| Contact US: help@patsnap.com