Method for producing functional soy peptide by alcohol leaching soy protein concentrate
A technology of concentrated soybean protein and soybean polypeptide, which is applied in the direction of protein food processing, plant protein processing, protein food ingredients, etc., can solve the problems that it is difficult to increase the total nitrogen content of the product, increase the difficulty of increasing soybean polypeptide, and it is difficult to deeply hydrolyze, etc., to achieve The effect of reducing the possibility of product contamination, shortening the processing time, and increasing the content of soluble nitrogen
- Summary
- Abstract
- Description
- Claims
- Application Information
AI Technical Summary
Problems solved by technology
Method used
Examples
Embodiment 1
[0031] A method for producing functional soybean polypeptides using alcohol-process soybean protein concentrate, the specific implementation steps are as follows:
[0032] ((1) Raw material liquid preparation
[0033] Take 1 part of alcohol-processed soybean protein concentrate and 6-12 parts of distilled water according to the weight ratio, and mix them to form a uniform soybean protein concentrate slurry;
[0034] (2) Cellulase hydrolysis pretreatment
[0035] Use hydrochloric acid solution with a weight content of 1-20% to adjust the pH value of the soybean protein concentrate slurry to 4-6, add cellulase, the amount of enzyme added is 0.5%-2% of the weight of the alcohol-process soybean protein concentrate raw material, stir evenly, Enzymolysis at 40-50°C for 2-3 hours; centrifuge the cellulase treatment solution at 2000-5000 rpm for 5-10 minutes, remove the supernatant, and add the same volume of distilled water as the supernatant , stirred to become the primary pretrea...
Embodiment 2
[0053] (1) Preparation of raw material solution
[0054] Take 1kg of alcohol-processed soybean protein concentrate from Tianjin Shifa Guanhua Biotechnology Co., Ltd. and mix it with 9kg of distilled water, and stir to form a uniform soybean protein concentrate slurry;
[0055] (2) Cellulase hydrolysis pretreatment
[0056] Use hydrochloric acid solution with a weight content of 10% to adjust the pH value of the soybean protein concentrate slurry to 5.0, add cellulase, the amount of enzyme added is 1.5% of the weight of the alcohol-process soybean protein concentrate raw material, stir evenly, and enzymatically hydrolyze at 45°C 2 hours; centrifuge the cellulase treatment solution at 2000 rpm for 10 minutes, remove the supernatant, and add distilled water of the same volume as the supernatant, and stir to become the primary pretreatment solution of soybean protein concentrate;
[0057] (3) Ultra-high temperature transient pretreatment
[0058] The soybean protein concentrate ...
Embodiment 3
[0070] (1) Preparation of raw material solution
[0071] Take 1kg of Soybean Milk from Yihai (Fangchenggang) Soybean Industry Co., Ltd. and mix it with 10kg of distilled water to form a uniform soybean protein concentrate slurry;
[0072] (2) Cellulase hydrolysis pretreatment
[0073] Use 10% hydrochloric acid solution by weight to adjust the pH value of the concentrated soybean protein slurry to 5.0, add cellulase, the amount of enzyme added is 2% of the weight of the raw material of concentrated soybean protein by alcohol method, stir evenly, and enzymatically hydrolyze at 50°C 3 hours; centrifuge the cellulase treatment solution at 5000 rpm for 6 minutes, remove the supernatant, and add distilled water of the same volume as the supernatant, and stir to become the primary pretreatment solution of soybean protein concentrate;
[0074] (3) Ultra-high temperature transient pretreatment
[0075] The soybean protein concentrate primary pretreatment liquid is subjected to ultra-...
PUM
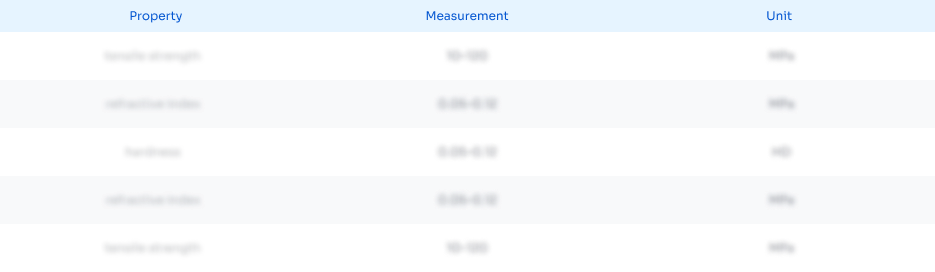
Abstract
Description
Claims
Application Information

- Generate Ideas
- Intellectual Property
- Life Sciences
- Materials
- Tech Scout
- Unparalleled Data Quality
- Higher Quality Content
- 60% Fewer Hallucinations
Browse by: Latest US Patents, China's latest patents, Technical Efficacy Thesaurus, Application Domain, Technology Topic, Popular Technical Reports.
© 2025 PatSnap. All rights reserved.Legal|Privacy policy|Modern Slavery Act Transparency Statement|Sitemap|About US| Contact US: help@patsnap.com