Method for compensating central point of double-turntable five-axis linked numerical control machining rotary tool
A five-axis linkage, rotating tool technology, applied in the direction of program control, computer control, general control system, etc., can solve the problem that the correction processing method cannot be universal, and the nonlinear motion error is difficult to correct.
- Summary
- Abstract
- Description
- Claims
- Application Information
AI Technical Summary
Problems solved by technology
Method used
Image
Examples
Embodiment Construction
[0078] The above solution will be further described below in conjunction with specific embodiments. It should be understood that these examples are used to illustrate the present invention and not to limit the scope of the present invention. The implementation conditions used in the examples can be further adjusted according to the conditions of specific manufacturers, and the implementation conditions not indicated are usually the conditions in routine experiments.
[0079] Example Example of Center Point Compensation of Rotary Tool for CNC Milling Machine
[0080] This embodiment is tested on a CNC milling machine in the laboratory. The compensation method is to calculate the rotation compensation vector, and calculate the output displacement according to the initial information of the tool position and the coordinate position calculated by linear interpolation, so as to realize the suppression of the abnormality of the five-axis machining CNC system. Linear motion error. ...
PUM
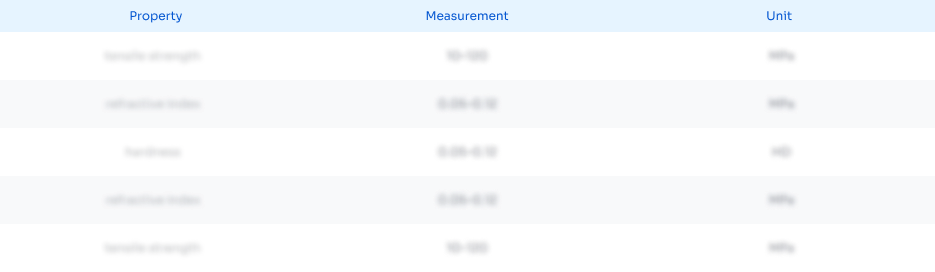
Abstract
Description
Claims
Application Information

- R&D
- Intellectual Property
- Life Sciences
- Materials
- Tech Scout
- Unparalleled Data Quality
- Higher Quality Content
- 60% Fewer Hallucinations
Browse by: Latest US Patents, China's latest patents, Technical Efficacy Thesaurus, Application Domain, Technology Topic, Popular Technical Reports.
© 2025 PatSnap. All rights reserved.Legal|Privacy policy|Modern Slavery Act Transparency Statement|Sitemap|About US| Contact US: help@patsnap.com