Method for preparing dicyanomethyl phenylphosphine
A technology of cyanomethylphenylphosphine and dicyanomethylphenyl, which is applied in chemical instruments and methods, compounds of Group 5/15 elements of the periodic table, organic chemistry, etc., can solve environmental pollution of waste residues and low yield and other problems, to achieve the effect of less by-products, simple production process, and obvious environmental protection
- Summary
- Abstract
- Description
- Claims
- Application Information
AI Technical Summary
Problems solved by technology
Method used
Image
Examples
Embodiment 1
[0021] Install a reactor, add 1 mole of zinc powder and 30 moles of tetrahydrofuran to the reactor under nitrogen protection, and then dropwise add a mixture of 1 mole of phenylphosphorus dichloride, 2.2 moles of bromoacetonitrile and 5 moles of tetrahydrofuran at room temperature , the dropwise addition time was 1 hour, and the reaction was stirred at room temperature for 2 hours after the dropwise addition was completed. After the reaction, the temperature of the solution in the reactor was raised to 50° C., and then the tetrahydrofuran and bromoacetonitrile in the solution were distilled off under a pressure of 60 mmHg. After steaming, add 10 moles of dichloromethane and 5 moles of water to the reactor, stir well, then stand for stratification, extract the upper organic layer, and then distill the organic layer at 60 mmHg and room temperature to remove the dichloride. After methane, the finished product of biscyanomethylphenylphosphine is obtained. After testing, the melti...
Embodiment 2
[0024] A reactor was installed, 1 mole of zinc powder and 30 moles of tetrahydrofuran were added to the reactor under nitrogen protection, and then a mixture of 1 mole of phenylphosphorus dichloride, 2.4 moles of bromoacetonitrile and 5 moles of tetrahydrofuran was added dropwise at a constant speed at 60 °C. The dropwise addition time was 1.5 hours. After the dropwise addition was completed, the reaction was stirred at 60° C. for 2 hours. After the reaction, the temperature of the solution in the reactor was kept at 60° C., and then the tetrahydrofuran and bromoacetonitrile in the solution were distilled off under a pressure of 60 mmHg. After steaming, add 10 moles of dichloromethane and 5 moles of water to the reactor, stir well, then stand for stratification, extract the upper organic layer, and then distill the organic layer at 60 mmHg and room temperature to remove the dichloride. After methane, the finished product of biscyanomethylphenylphosphine is obtained. After tes...
Embodiment 3
[0027] A reactor was installed, 1 mole of zinc powder and 10 moles of tetrahydrofuran were added to the reactor under nitrogen protection, and then a mixture of 1 mole of phenylphosphorus dichloride, 2 moles of bromoacetonitrile and 10 moles of tetrahydrofuran was added dropwise at a constant speed at 70 °C. The dropwise addition time was 2 hours. After the dropwise addition was completed, the reaction was stirred at 70° C. for 3 hours. After the reaction, the temperature of the solution in the reactor was kept at 70°C, and then the tetrahydrofuran and bromoacetonitrile in the solution were distilled off under a pressure of 60 mmHg. After steaming, add 10 moles of dichloromethane and 5 moles of water to the reactor, stir well, then stand for stratification, extract the upper organic layer, and then distill the organic layer at 60 mmHg and room temperature to remove the dichloride. After methane, the finished product of biscyanomethylphenylphosphine is obtained. After testing,...
PUM
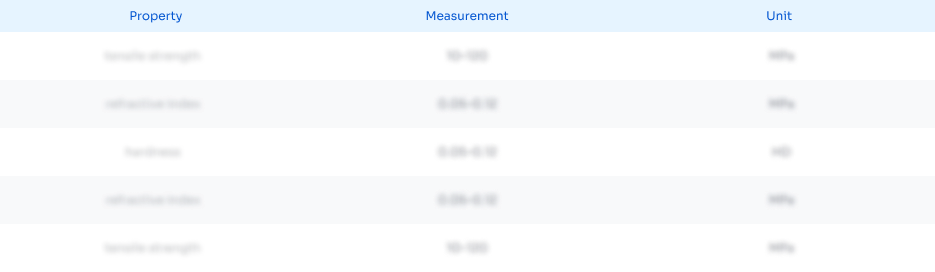
Abstract
Description
Claims
Application Information

- R&D
- Intellectual Property
- Life Sciences
- Materials
- Tech Scout
- Unparalleled Data Quality
- Higher Quality Content
- 60% Fewer Hallucinations
Browse by: Latest US Patents, China's latest patents, Technical Efficacy Thesaurus, Application Domain, Technology Topic, Popular Technical Reports.
© 2025 PatSnap. All rights reserved.Legal|Privacy policy|Modern Slavery Act Transparency Statement|Sitemap|About US| Contact US: help@patsnap.com