Material separator for circulating fluidized bed boiler
A circulating fluidized bed and separator technology, which is applied to fluidized bed combustion equipment, separation methods, dispersed particle separation, etc., can solve the problems of slow start and stop of boilers, large amount of fly ash, and high concentration of smoke and dust, and achieve extended use. life, improve overall energy efficiency, and reduce smoke and dust emissions
- Summary
- Abstract
- Description
- Claims
- Application Information
AI Technical Summary
Problems solved by technology
Method used
Image
Examples
Embodiment 1
[0024] see figure 1 , figure 2 , a circulating fluidized bed boiler material separator, which is characterized in that the inlet and outlet of the turning channel form a tube bundle that is conducive to the uniform flow and collision inertial separation of smoke and dust. Its specific structure includes a front downward flue 8, a flue gas inlet 6, a turning channel 20, a silo 21, a flue gas outlet 19, a rear upward flue 16, etc. The material separator is arranged at the rear of the furnace 1 to guide the flue gas downwards and upwards. The folding membrane screen 9 is in the middle or front of the furnace rear wall 2 and the shaft flue front wall 18 or the front convection tube bundle 35, and the space between them is divided into the front descending flue 8 and the rear ascending flue 16, The front part of the fork 7 at the lower end of the guiding flue gas is the flue gas inlet 6, and the rear part is the flue gas outlet 19, and the upper part from the fork 7 to the upper ...
Embodiment 2
[0030] see image 3 , Figure 4 , and the difference from Embodiment 1 is that: at the lower part of the membrane screen bifurcation 7, two rows of tube bundles are formed on the turning channel. The specific structure is: the lower part of the membrane-type screen bifurcation 7 divides two rows of tube bundles with thin spacing, the lower end of the front row of tube bundles 36 communicates with the upper center of the horizontal header 38 under the membrane-type screen, and the rear row of tube bundles 37 is a certain distance away from the front row of tube bundles 36 , its lower end is in radial communication with the rear wall of the horizontal header 38 under the membrane screen, the upper end of the front wall support plate 39 of the feed bin is closely sealed against the rear wall of the furnace, its lower end is close to the outer side of the upper end of the material leg 24, and its inner side is tightly sealed. It is sealed with a refractory insulation wall; the up...
PUM
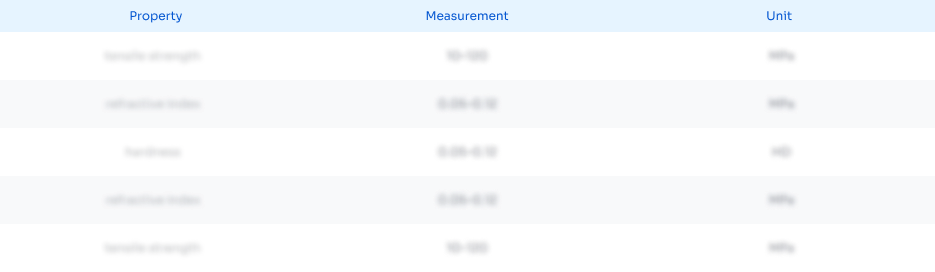
Abstract
Description
Claims
Application Information

- R&D
- Intellectual Property
- Life Sciences
- Materials
- Tech Scout
- Unparalleled Data Quality
- Higher Quality Content
- 60% Fewer Hallucinations
Browse by: Latest US Patents, China's latest patents, Technical Efficacy Thesaurus, Application Domain, Technology Topic, Popular Technical Reports.
© 2025 PatSnap. All rights reserved.Legal|Privacy policy|Modern Slavery Act Transparency Statement|Sitemap|About US| Contact US: help@patsnap.com