Redundant parallel six-dimensional acceleration transducer and measuring method thereof
An acceleration sensor, parallel technology, applied in the field of measurement, can solve the problems of sensitivity and range to be improved, time-consuming parallel mechanism, constraining the response frequency of the acceleration sensor, etc., to achieve high stiffness, large carrying capacity, and improve the effect of measurement accuracy
- Summary
- Abstract
- Description
- Claims
- Application Information
AI Technical Summary
Problems solved by technology
Method used
Image
Examples
Embodiment Construction
[0035] The structure and working process of the present invention will be described in detail below in conjunction with the accompanying drawings and specific embodiments.
[0036] first reference figure 1 As shown, the present invention provides a redundant parallel six-dimensional acceleration sensor, which includes a housing 3, a mass 5 and 3 sets of elastic hinge devices, which will be introduced separately below.
[0037] The casing 3 is a rigid structure, designed as a T-shaped structure in this embodiment, having a plate-shaped horizontal part and a cubic-shaped vertical part, and an accommodating cavity 31 is opened in the vertical part.
[0038] The mass block 5 is a cube, and is arranged in the accommodating cavity 31 of the housing 3 .
[0039] The three sets of elastic hinge devices are all arranged in the accommodating chamber 31 of the housing 3, wherein one end of the three sets of elastic hinge devices are respectively fixed on the center of three adjacent and...
PUM
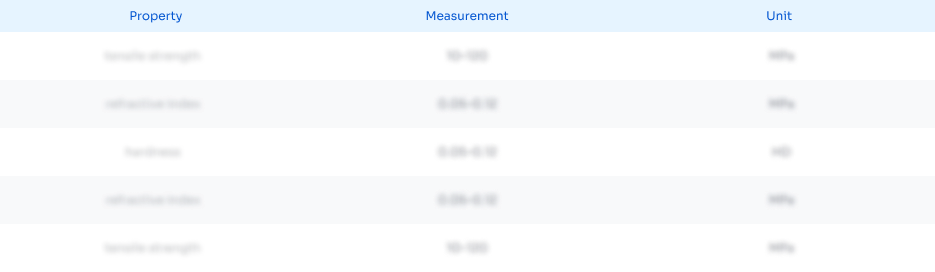
Abstract
Description
Claims
Application Information

- R&D Engineer
- R&D Manager
- IP Professional
- Industry Leading Data Capabilities
- Powerful AI technology
- Patent DNA Extraction
Browse by: Latest US Patents, China's latest patents, Technical Efficacy Thesaurus, Application Domain, Technology Topic, Popular Technical Reports.
© 2024 PatSnap. All rights reserved.Legal|Privacy policy|Modern Slavery Act Transparency Statement|Sitemap|About US| Contact US: help@patsnap.com