Regeneration method of catalyst for dehydrogenation of low-carbon alkanes
A technology for dehydrogenation catalysts and low-carbon alkanes, which is applied in the direction of catalyst regeneration/reactivation, hydrocarbons, hydrocarbons, etc., and can solve the problems of active metal accumulation, long regeneration time, and easy change of catalyst crystal form
- Summary
- Abstract
- Description
- Claims
- Application Information
AI Technical Summary
Problems solved by technology
Method used
Image
Examples
Embodiment 1
[0027] The deactivated Pt-Sn-K / Al described in Comparative Example 2 2 o 3 Catalyst, loaded in a micro-inverted fixed-bed reactor, the catalyst loading is 10ml, the first step is to feed air, the air flow rate is controlled to be 60 g / h, the regeneration temperature is 400 ° C, and the regeneration time is 2 hours; the second step is to feed water Steam and air mixture, control the water vapor flow rate to 40 g / h, the air flow rate to 60 g / h, and the regeneration temperature to 460°C, to carry out the catalyst regeneration test, and the regeneration time is 1 hour.
Embodiment 2
[0029] The deactivated Pt-Sn-K / Al described in Comparative Example 2 2 o 3 Catalyst, loaded in a micro-inverted fixed-bed reactor, the loading amount of the catalyst is 10ml, the first step is to feed air, the air flow rate is controlled to be 60 g / h, the regeneration temperature is 420 ° C, and the regeneration time is 2 hours; the second step is to feed water Steam and air mixture, control the water vapor flow rate to 40 g / hour, the air flow rate to 60 g / hour, and the regeneration temperature to 480°C to carry out the catalyst regeneration test, and the regeneration time is 1 hour.
Embodiment 3
[0031] The deactivated Pt-Sn-K / Al described in Comparative Example 2 2 o 3 Catalyst, loaded in a micro-inverted fixed-bed reactor, the catalyst loading is 10ml, the first step is to feed air, the air flow rate is controlled to be 60 g / h, the regeneration temperature is 380 ° C, and the regeneration time is 3 hours; the second step is to feed water Steam and air mixture, control the water vapor flow rate to 20 g / h, the air flow rate to 80 g / h, and the regeneration temperature to 430°C, to carry out the catalyst regeneration test, and the regeneration time is 2 hours.
PUM
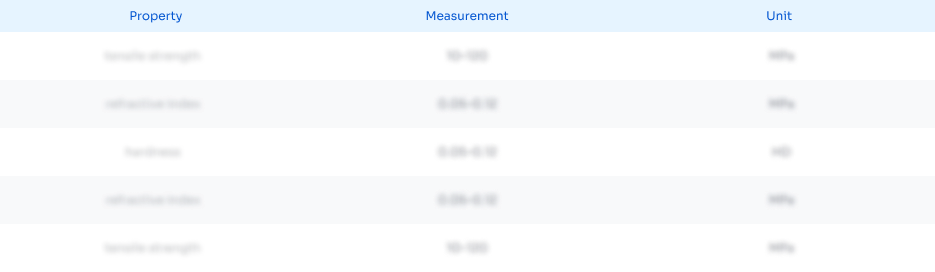
Abstract
Description
Claims
Application Information

- R&D
- Intellectual Property
- Life Sciences
- Materials
- Tech Scout
- Unparalleled Data Quality
- Higher Quality Content
- 60% Fewer Hallucinations
Browse by: Latest US Patents, China's latest patents, Technical Efficacy Thesaurus, Application Domain, Technology Topic, Popular Technical Reports.
© 2025 PatSnap. All rights reserved.Legal|Privacy policy|Modern Slavery Act Transparency Statement|Sitemap|About US| Contact US: help@patsnap.com