Method and apparatus for manufacturing inner ring and outer ring
A manufacturing method and technology of inner and outer rings, applied in the direction of engine components, mechanical equipment, etc., can solve the problems of material waste, low yield, high material cost, etc., and achieve the effects of reducing forming load, easy manufacturing, and reducing forming load
- Summary
- Abstract
- Description
- Claims
- Application Information
AI Technical Summary
Problems solved by technology
Method used
Image
Examples
Embodiment Construction
[0058] Hereinafter, embodiments of the present invention will be described in detail with reference to the drawings.
[0059] Figure 1 to Figure 6 The manufacturing process of the ball bearing composed of the outer ring R2 and the inner ring R1 is shown step by step.
[0060] figure 1 It represents one cylindrical raw material A cut into a predetermined size after heating. The cylindrical raw material A is obtained by sending a heated round bar wire with a predetermined size to the front side of a die block by a transfer device in a multi-stage thermoforming facility, and cutting it into a predetermined size with a cutting knife.
[0061] The columnar material A was subjected to upsetting in a thermoforming facility. Formed by this upsetting process such as figure 2 The disc-shaped raw material B with the arc-shaped outer peripheral surface is shown. Then, the disk-shaped raw material B is transferred to the first process of the thermoforming equipment. In addition, t...
PUM
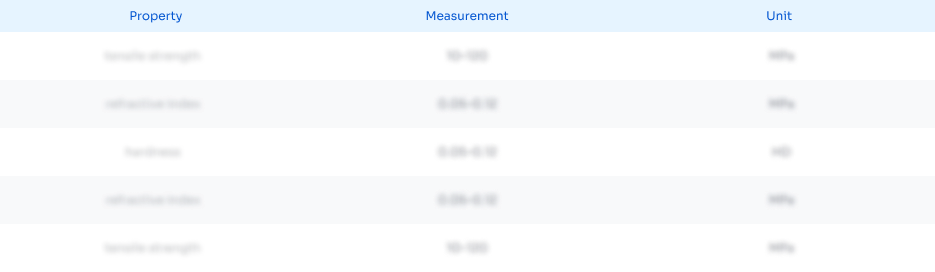
Abstract
Description
Claims
Application Information

- R&D
- Intellectual Property
- Life Sciences
- Materials
- Tech Scout
- Unparalleled Data Quality
- Higher Quality Content
- 60% Fewer Hallucinations
Browse by: Latest US Patents, China's latest patents, Technical Efficacy Thesaurus, Application Domain, Technology Topic, Popular Technical Reports.
© 2025 PatSnap. All rights reserved.Legal|Privacy policy|Modern Slavery Act Transparency Statement|Sitemap|About US| Contact US: help@patsnap.com