Dry-mixed mortar with heat insulation function and preparation process thereof
A dry-mixed mortar, thermal insulation technology, applied in the field of building materials, can solve the problems that additives are not easy to disperse uniformly to wrap aggregate, lightweight aggregate is easy to layer and float, and is not easy to disperse, etc., to achieve excellent construction operability, heat insulation Remarkable thermal insulation effect and good anti-sag performance
- Summary
- Abstract
- Description
- Claims
- Application Information
AI Technical Summary
Problems solved by technology
Method used
Image
Examples
Embodiment 1
[0027] by 1m 3 To calculate the finished product, weigh 120 kg of expanded vitrified microbeads, 160 kg of 42.5 grade cement, 3 kg of wood fiber, 1 kg of hydroxypropyl methylcellulose, 6 kg of redispersible rubber powder and 0.5 kg of polypropylene short fiber.
[0028] When mixing with figure 1 For the mixing equipment shown, 160 kg of 42.5 grade cement, 3 kg of wood fiber, 1 kg of hydroxypropyl methyl cellulose, 6 kg of redispersible rubber powder and 0.5 kg of polypropylene short fiber are lifted to the storage through the feeding part 10. In the silo 21, open the outlet of the storage silo 21 so that the material is injected into the closed mixing chamber 22, and the horizontally designed spiral agitator 24 in the closed mixing chamber 22 is rotated and stirred to realize the material in the closed material convection mixing area. Mixing is completed within 5 minutes, and the mixing time is 5 minutes; when other raw materials other than the expanded vitrified microspheres...
Embodiment 2
[0030] by 1m 3 To calculate the finished product, weigh 110kg of expanded vitrified microbeads, 160kg of grade 42.5 cement, 3.5 kg of wood fiber, 1 kg of hydroxypropyl methylcellulose, 5 kg of redispersible rubber powder and 0.5 kg of polypropylene short fiber.
[0031] The mixing process was the same as in Example 1, except that the mixing time for other raw materials other than the expanded vitrified microbeads was 5 minutes, and the continuous mixing time after adding the expanded vitrified microbeads was 50 seconds, and the rest of the work will not be repeated here.
Embodiment 3
[0033] by 1m 3 To calculate the finished product, weigh 115 kg of expanded vitrified microbeads, 150 kg of 42.5 grade cement, 3.5 kg of wood fiber, 1.5 kg of hydroxypropyl methylcellulose, 6 kg of redispersible rubber powder and 0.5 kg of polypropylene short fiber.
[0034] The mixing process was the same as in Example 1, except that the mixing time for other raw materials other than the expanded vitrified microbeads was 4 minutes, and the continuous mixing time after adding the expanded vitrified microbeads was 60 seconds, and the rest of the work will not be repeated here.
PUM
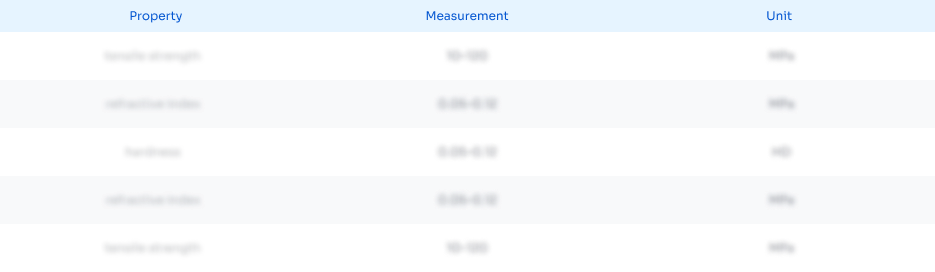
Abstract
Description
Claims
Application Information

- R&D
- Intellectual Property
- Life Sciences
- Materials
- Tech Scout
- Unparalleled Data Quality
- Higher Quality Content
- 60% Fewer Hallucinations
Browse by: Latest US Patents, China's latest patents, Technical Efficacy Thesaurus, Application Domain, Technology Topic, Popular Technical Reports.
© 2025 PatSnap. All rights reserved.Legal|Privacy policy|Modern Slavery Act Transparency Statement|Sitemap|About US| Contact US: help@patsnap.com