Oil-gas lubricating oil and production method thereof
A production method and lubricating oil technology, which is applied in the field of lubricating oil, can solve the problems of single type of oil and gas lubricating oil base oil, poor cleaning performance of the system, avoiding coking, etc., achieve strong cleaning performance, prevent clogging of oil pipelines, and are not easy to coke Effect
- Summary
- Abstract
- Description
- Claims
- Application Information
AI Technical Summary
Problems solved by technology
Method used
Image
Examples
Embodiment 1
[0048] Step a) mix 80% by weight polyether NPE-108 and 14.98% polyol ester base oil produced by Dongxu Chemical Factory in Yingkou City, and send it into the blending kettle with a gear pump, evacuate, stir, heat, and heat up to 75°C;
[0049] Step b) Add 2% T501 (2,6-di-tert-butyl p-cresol), 0.01% sodium petroleum sulfonate, 2% thiadiazole, 1% phosphoric acid to the base oil obtained in step a) Tricresyl ester and 0.01% 10000# methyl silicone oil, continue to heat up to 100°C, dehydrate at -0.08MPa, then cool down to below 75°C, stop evacuation and stirring;
[0050] Step c) filter the oil product obtained in step b), the specific filtration process is: take out a small amount of the oil product obtained in step b), add 0.02% of the weight of all the oil product diatomite filter aid to stir, and perform circulating filtration After the filter aid forms a filter cake in the filter machine, the remaining oil in the kettle is circulated and filtered until the oil is clear and t...
Embodiment 2
[0052] Step a) mix 75% by weight polyether NPE-105 and 17% heavy alkylbenzene, and send it into the preparation kettle with a gear pump, evacuate, stir, heat, and raise the temperature to 80°C;
[0053] Step b) Add 3% ZDDP (zinc dialkyl dithiophosphate), 1.95% barium dinonyl naphthalene sulfonate, 1% palmitic acid, 2% phosphorous acid to the base oil obtained in step a) Dibutyl ester and 0.05% polydimethylsiloxane, continue to heat up to 110°C, dehydrate at -0.09MPa, then cool down to 65°C, stop evacuation and stirring;
[0054] Step c) filtering the oil product obtained in step b), the specific filtration process is: taking a small amount of the oil product obtained in step b), adding 0.03% perlite filter aid of all oil products and stirring, performing circulating filtration, After the filter aid forms a filter cake in the filter machine, the remaining oil in the kettle is circulated and filtered until the oil is clear and transparent without mechanical impurities, and oil-g...
Embodiment 3
[0056] Step a) Mix 85% polyether F-6 and 8% alkylnaphthalene by weight and send it into the preparation kettle with a gear pump, evacuate, stir, heat, and raise the temperature to 85°C;
[0057] Step b) Add 1% of dialkyldiphenylamine, 2% of sodium heavy alkylbenzene sulfonate, 2% of T406 (benzotriazole fatty acid amine salt), 1.5% of the base oil obtained in step a) Molybdenum dialkyldithiocarbamate and 0.5% polymethacrylate, continue to heat up to 120°C, dehydrate at -0.07MPa, then cool down to below 65°C, stop evacuation and stirring;
[0058] Step c) filter the oil product obtained in step b), the specific filtration process is: take out a small amount of the oil product obtained in step b), add 0.04% of the activated carbon filter aid of all the oil product weight and stir, carry out circulating filtration, make After the filter aid forms a filter cake in the filter machine, the remaining oil in the kettle is circulated and filtered until the oil is clear and transparent w...
PUM
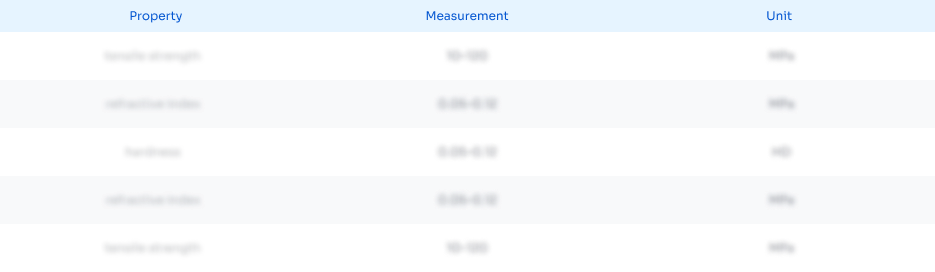
Abstract
Description
Claims
Application Information

- R&D
- Intellectual Property
- Life Sciences
- Materials
- Tech Scout
- Unparalleled Data Quality
- Higher Quality Content
- 60% Fewer Hallucinations
Browse by: Latest US Patents, China's latest patents, Technical Efficacy Thesaurus, Application Domain, Technology Topic, Popular Technical Reports.
© 2025 PatSnap. All rights reserved.Legal|Privacy policy|Modern Slavery Act Transparency Statement|Sitemap|About US| Contact US: help@patsnap.com