Divided-flow secondary injection flow passage device of ejection forming machine
A two-stage injection and shunt-type technology, applied in the field of injection molding, can solve the problems of unqualified products, lower production efficiency, retention and other problems, achieve the effect of wide process adjustment range, solve residual material retention, and improve production efficiency
- Summary
- Abstract
- Description
- Claims
- Application Information
AI Technical Summary
Problems solved by technology
Method used
Image
Examples
Embodiment Construction
[0023] Below, with reference to the accompanying drawings and specific implementation methods, the split-type secondary injection channel device of the injection molding machine of the present invention will be further described, so as to better understand the technical idea claimed by the present invention.
[0024] Such as figure 2 , 3 , 4, is a split-type two-stage injection channel device for an injection molding machine of the present invention, which includes a barrel nozzle 21, a channel connector 22, a conversion seat 23, an injection cylinder 24, and a channel switching valve 26 , Injection nozzle 25, wherein, the flow channel connecting body 22 is connected between the output end of the barrel nozzle 21 and the conversion seat 23, and the inner cavities of the three are conductively connected, specifically, the flow channel connecting body 22 The inner cavity is in the shape of a "herringbone", the upper end of the "herringbone" is connected to the output end of th...
PUM
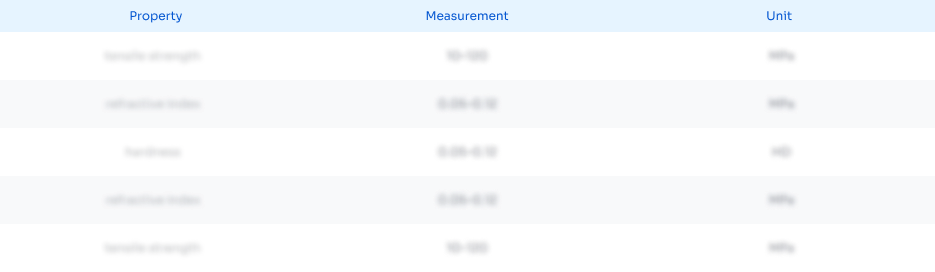
Abstract
Description
Claims
Application Information

- R&D
- Intellectual Property
- Life Sciences
- Materials
- Tech Scout
- Unparalleled Data Quality
- Higher Quality Content
- 60% Fewer Hallucinations
Browse by: Latest US Patents, China's latest patents, Technical Efficacy Thesaurus, Application Domain, Technology Topic, Popular Technical Reports.
© 2025 PatSnap. All rights reserved.Legal|Privacy policy|Modern Slavery Act Transparency Statement|Sitemap|About US| Contact US: help@patsnap.com