Oil-washing deep processing technology of coal tar
A technology for deep processing and coal tar, applied in the field of chemical engineering, can solve the problems of many separation methods, complicated operation process, single separation component, etc., and achieve the effect of reducing production cost, high economic value and convenient operation.
- Summary
- Abstract
- Description
- Claims
- Application Information
AI Technical Summary
Problems solved by technology
Method used
Image
Examples
Embodiment 1
[0018] As shown in the figure, the rectifying equipment of the present invention consists of a washing tower and eight rectifying towers. The wash oil fraction is a distillate with a distillation range of 230°C to 300°C. The washing oil fraction first passes into the washing tower through pickling and alkali cleaning process (the pickling and alkali washing method adopts the pickling and alkali washing method in the prior art), so that more than 99.0% of the quinolines are removed, and enter the naphthalene washing, Separation tower 2. The naphthalene washing and separation tower is composed of 80 trays, the raw material is added from the 40th tray, the flow rate is 3556kg / hr, the tower top pressure is 5Kpa, the tower top temperature is 130°C, and the reflux ratio is 5. Naphthalene with a concentration of more than 99.5% is produced at the top of the tower, and the bottom fraction enters the methylnaphthalene tower 3 . The methylnaphthalene tower is composed of 80 trays, the...
Embodiment 2
[0020] As shown in the figure, the rectifying equipment of the present invention consists of a washing tower and eight rectifying towers. The wash oil fraction is a distillate with a distillation range of 230°C to 300°C. The washing oil fraction first passes into the washing tower through pickling and alkali cleaning process (the pickling and alkali washing method adopts the pickling and alkali washing method in the prior art), so that more than 99.0% of the quinolines are removed, and enter the naphthalene washing, Separation tower 2. The naphthalene washing and separation tower is composed of 78 trays, the raw material is added from the 39th tray, the flow rate is 3556kg / hr, the reflux ratio is 4, the temperature at the top of the tower is 135°C, and the pressure at the top of the tower is 10KPa. Naphthalene with a concentration exceeding 99.6% is produced at the top of the tower, and the bottom fraction enters the methylnaphthalene tower 3 . The methylnaphthalene tower is...
Embodiment 3
[0022]As shown in the figure, the rectifying equipment of the present invention consists of a washing tower and eight rectifying towers. The wash oil fraction is a distillate with a distillation range of 230°C to 300°C. The washing oil fraction first passes into the washing tower through pickling and alkali cleaning process (the pickling and alkali washing method adopts the pickling and alkali washing method in the prior art), so that more than 99.0% of the quinolines are removed, and enter the naphthalene washing, Separation tower 2. The naphthalene washing and separation tower is composed of 74 trays, the raw material is fed from the 37th tray, the flow rate is 3556kg / hr, the reflux ratio is 6, the temperature at the top of the tower is 138°C, and the pressure at the top of the tower is 20KPa. Naphthalene with a concentration exceeding 99.4% is produced at the top of the tower, and the bottom fraction enters the methylnaphthalene tower 3 . The methylnaphthalene tower is co...
PUM
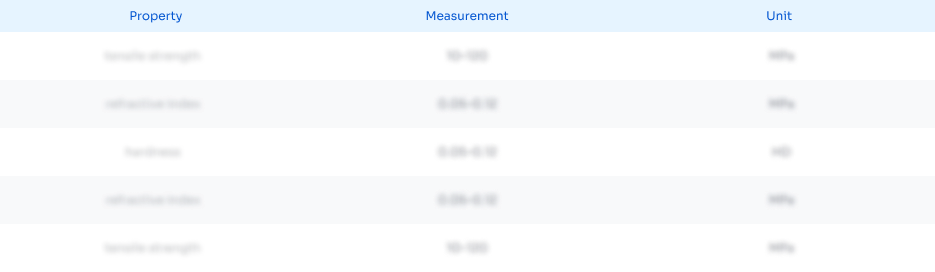
Abstract
Description
Claims
Application Information

- R&D
- Intellectual Property
- Life Sciences
- Materials
- Tech Scout
- Unparalleled Data Quality
- Higher Quality Content
- 60% Fewer Hallucinations
Browse by: Latest US Patents, China's latest patents, Technical Efficacy Thesaurus, Application Domain, Technology Topic, Popular Technical Reports.
© 2025 PatSnap. All rights reserved.Legal|Privacy policy|Modern Slavery Act Transparency Statement|Sitemap|About US| Contact US: help@patsnap.com