One-step molding support member production process
A molding support and production process technology, applied in the direction of coil manufacturing, etc., can solve the problems of affecting the withstand voltage performance, complicated processing methods, and low production efficiency, and achieve the goals of improving electrical insulation performance, reducing secondary pollution, and reducing labor productivity. Effect
- Summary
- Abstract
- Description
- Claims
- Application Information
AI Technical Summary
Problems solved by technology
Method used
Image
Examples
Embodiment 1
[0007] Embodiment 1: as figure 1 As shown, the wood pulp is purified and pretreated, then pulped and crushed, concentrated to a concentration of 4.0±0.5%, and then enters the coarse stock tank, and the pulp is sent to the refiner through the pulp pump. The refined pulp is sent to the pulp tank , and then sent to the high-efficiency low-consistency slag remover through the pulp pump. After the slag is removed, it enters the pulp stabilization box, and then is sent to the wet paper blank forming device through the pulp pump, and the wet paper blank is sent into the mold with the inner net , together with the mold, sent to the hot press machine to squeeze water, dry, the temperature is 120±5°C, the drying time depends on the thickness, dry to the moisture content of the cardboard 4-6%, unload the board and enter the semi-finished product room for 3-5 days, and then Finishing and trimming are carried out, and after inspection, vacuum packaging is put into storage.
PUM
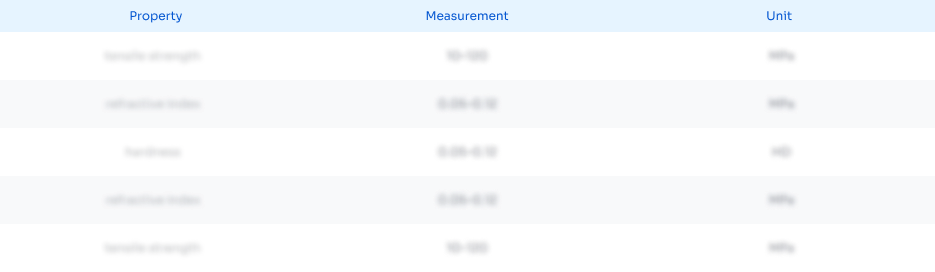
Abstract
Description
Claims
Application Information

- R&D Engineer
- R&D Manager
- IP Professional
- Industry Leading Data Capabilities
- Powerful AI technology
- Patent DNA Extraction
Browse by: Latest US Patents, China's latest patents, Technical Efficacy Thesaurus, Application Domain, Technology Topic, Popular Technical Reports.
© 2024 PatSnap. All rights reserved.Legal|Privacy policy|Modern Slavery Act Transparency Statement|Sitemap|About US| Contact US: help@patsnap.com