Method for manufacturing hammer lever of electrohydraulic hammer
A manufacturing method and technology of electro-hydraulic hammer, which are applied in the direction of manufacturing tools, coatings, furnace types, etc., can solve the problems of breakage and failure of hammer rods, and achieve the effect of improving service life
- Summary
- Abstract
- Description
- Claims
- Application Information
AI Technical Summary
Problems solved by technology
Method used
Image
Examples
Embodiment 1
[0036] as per figure 1 The flow shown, its manufacturing process is as follows:
[0037] (1) Material selection, the forging material obtained by electroslag steel smelting is selected as the forging blank, and the surface of the forging blank is peeled before flaw detection. The material of the forging material obtained by electroslag steel smelting is 42CrMo, which is mainly selected It has the following advantages: one is that the material cost is reduced by about 3 / 4, and the other is that the material has high strength, hardenability, good toughness, small deformation during quenching, and high creep strength and durability at high temperature; It is guaranteed that no cracks affecting the strength are allowed inside and on the surface of the forging blank, and no scratches are allowed on the surface, and the ultrasonic flaw detection defect equivalent should be ≤Ф2. The principle of material selection is to make the optimal choice according to the above requirements und...
Embodiment 2
[0050] as per figure 1 The flow shown, its manufacturing process is as follows:
[0051] (1) Material selection, the forging material obtained by electroslag steel smelting is selected as the forging blank, and the surface of the forging blank is peeled before flaw detection. The material of the forging material obtained by electroslag steel smelting is 42CrMo, which is mainly selected It has the following advantages: one is that the material cost is reduced by about 3 / 4, and the other is that the material has high strength, hardenability, good toughness, small deformation during quenching, and high creep strength and durability at high temperature; It is guaranteed that no cracks affecting the strength are allowed inside and on the surface of the forging blank, and no scratches are allowed on the surface, and the ultrasonic flaw detection defect equivalent should be ≤Ф2. The principle of material selection is to make the optimal choice according to the above requirements und...
Embodiment 3
[0063] as per figure 1 The flow shown, its manufacturing process is as follows:
[0064] (1) Material selection, the forging material obtained by electroslag steel smelting is selected as the forging blank, and the surface of the forging blank is peeled before flaw detection. The material of the forging material obtained by electroslag steel smelting is 42CrMo, which is mainly selected It has the following advantages: one is that the material cost is reduced by about 3 / 4, and the other is that the material has high strength, hardenability, good toughness, small deformation during quenching, high creep strength and durable strength at high temperature; after flaw detection, it should be guaranteed Any cracks affecting the strength are not allowed inside and on the surface of the forging blank, and scratches are not allowed on the surface, and the ultrasonic flaw detection defect equivalent should be ≤Ф2. The principle of material selection is to make the optimal choice accordi...
PUM
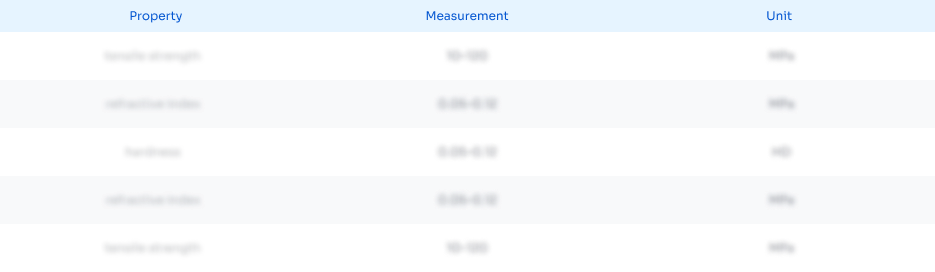
Abstract
Description
Claims
Application Information

- Generate Ideas
- Intellectual Property
- Life Sciences
- Materials
- Tech Scout
- Unparalleled Data Quality
- Higher Quality Content
- 60% Fewer Hallucinations
Browse by: Latest US Patents, China's latest patents, Technical Efficacy Thesaurus, Application Domain, Technology Topic, Popular Technical Reports.
© 2025 PatSnap. All rights reserved.Legal|Privacy policy|Modern Slavery Act Transparency Statement|Sitemap|About US| Contact US: help@patsnap.com