Preparation method of green pigment for ceramic high-temperature glaze
A high-temperature glaze and green technology, applied in the field of preparation of ceramic pigments, can solve the problems of low tinting strength, short process flow, easy agglomeration, etc., and achieve the effect of pure color tone, simple process flow, and strong high temperature resistance
- Summary
- Abstract
- Description
- Claims
- Application Information
AI Technical Summary
Problems solved by technology
Method used
Examples
Embodiment 1
[0010] The raw materials used are all industrial pure, and the ingredients are formulated according to the following weight percentages, Cr 2 o 3 58%, Co. 2 o 3 10%, Fe 2 o 3 12%, Al 2 o 3 14%, ZnO6%. Put the raw materials into the wet ball mill in proportion, according to raw materials: ball: water = 1: 3: 1, grind for 48 to 72 hours, pass through a 250 mesh sieve, dehydrate and dry, roast at 1350°C, grind into powder after cooling, and then wash with water Dry until there is no variegated color.
Embodiment 2
[0012] The raw materials used are all industrial pure, according to the following proportions by weight, Cr 2 o 3 68%, Co. 2 o 3 5%, Fe 2 o 3 8%, Al 2 o 3 11%, ZnO8%. Put the raw materials into the wet ball mill in proportion, according to raw materials: ball: water = 1: 3: 1, grind for 48-72 hours, pass through a 250 mesh sieve, dehydrate and dry, roast at 1350 °C at high temperature, cool and grind into powder, and then use Wash with water until there is no variegation, then dry it for later use.
Embodiment 3
[0014] The raw materials used are all industrial pure, according to the following proportions by weight, Cr 2 o 3 64%, Co. 2 o 3 8%, Fe 2 o 3 11%, Al 2 o 3 12%, ZnO5%. Put the raw materials into the wet ball mill in proportion, according to raw materials: ball: water = 1: 3: 1, grind for 48 to 72 hours, pass through a 250 mesh sieve, dehydrate and dry, roast at 1350°C, grind into powder after cooling, and then wash with water Dry until there is no variegated color.
PUM
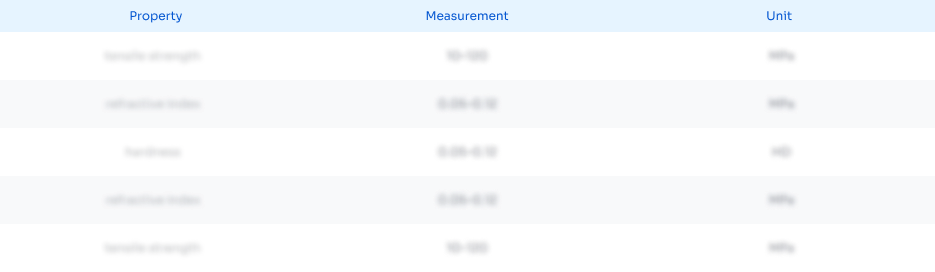
Abstract
Description
Claims
Application Information

- R&D Engineer
- R&D Manager
- IP Professional
- Industry Leading Data Capabilities
- Powerful AI technology
- Patent DNA Extraction
Browse by: Latest US Patents, China's latest patents, Technical Efficacy Thesaurus, Application Domain, Technology Topic, Popular Technical Reports.
© 2024 PatSnap. All rights reserved.Legal|Privacy policy|Modern Slavery Act Transparency Statement|Sitemap|About US| Contact US: help@patsnap.com