Polyurethane resin comprising alicyclic component and/or aromatic component and phase difference film using the polyurethane resin
A technology of polyurethane resin and phase difference film, which is applied in the field of polyurethane resin, can solve problems such as film thermal degradation, and achieve sufficient heat resistance without reducing the phase difference
- Summary
- Abstract
- Description
- Claims
- Application Information
AI Technical Summary
Problems solved by technology
Method used
Image
Examples
Embodiment 1
[0125] 45.2 parts by weight of 4,4'-dicyclohexylmethane diisocyanate was put into the reaction vessel, and 240 parts by weight of dimethylformamide was added to dissolve it. Next, stirring this solution, a solution of 24.8 parts by weight of 1,4-cyclohexanedimethanol dissolved in 40 parts by weight of dimethylformamide was slowly added. After completion of addition, reaction was performed at 130° C. for 4 hours, the reaction solution was poured into methanol, and the generated resin was deposited. The precipitated resin was vacuum-dried at 80°C.
[0126] The NMR spectrum of the resin produced in this way is shown in Figure 1. In addition, the evaluation results of heat resistance, molecular weight, optical properties, strength, and applicability are shown in Table 1.
Embodiment 2
[0128] 44.4 parts by weight of 4,4'-diphenylmethane diisocyanate was put into the reaction vessel, and 240 parts by weight of dimethylformamide was added to dissolve it. Next, stirring this solution, a solution of 25.59 parts by weight of 1,4-cyclohexanedimethanol dissolved in 40 parts by weight of dimethylformamide was slowly added. After completion of addition, reaction was performed at 130° C. for 4 hours, the reaction solution was poured into methanol, and the generated resin was deposited. The precipitated resin was vacuum-dried at 80°C.
[0129] Table 1 shows the evaluation results of heat resistance, molecular weight, optical properties, strength, and coatability of the resin thus prepared.
Embodiment 3
[0131] 21.28 parts by weight of 1,4-cyclohexanedimethanol was put into a reaction container, and 30 parts by weight of a solvent dimethylformamide was added, and it heated to 110 degreeC in nitrogen atmosphere. Next, 38.72 parts by weight of 4,4'-dicyclohexylmethane diisocyanate was added at a rate of 1 part by weight per minute, and 10 parts by weight of a solvent (dimethylformamide) was further added. After the addition was complete, a reaction was carried out at 130° C. for 23 hours. Next, the temperature of the reaction container was raised to 220° C., and the solvent was removed under a reduced pressure of about 5 Torr, and then the resin was extruded from the reaction container to form particles.
[0132] Table 1 shows the heat resistance, molecular weight, optical properties, strength, and coatability of the melt-extruded film of this resin.
PUM
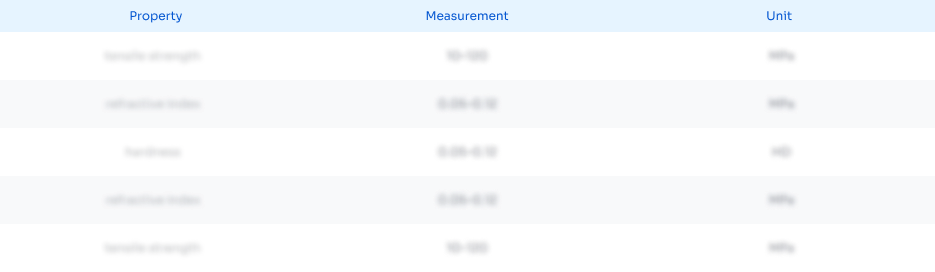
Abstract
Description
Claims
Application Information

- R&D Engineer
- R&D Manager
- IP Professional
- Industry Leading Data Capabilities
- Powerful AI technology
- Patent DNA Extraction
Browse by: Latest US Patents, China's latest patents, Technical Efficacy Thesaurus, Application Domain, Technology Topic, Popular Technical Reports.
© 2024 PatSnap. All rights reserved.Legal|Privacy policy|Modern Slavery Act Transparency Statement|Sitemap|About US| Contact US: help@patsnap.com