Method for preparing fluid loss additive for drilling fluid
A technology of fluid loss reducer and drilling fluid, which is applied in drilling compositions, chemical instruments and methods, etc., can solve problems such as troubles and risks in production, difficulty in compatibility of retarders and accelerators, etc., and achieve drilling efficiency High, good salt resistance, low filtration effect
- Summary
- Abstract
- Description
- Claims
- Application Information
AI Technical Summary
Problems solved by technology
Method used
Image
Examples
Embodiment 1
[0039] Prepared in parts by weight, take 30 parts of sodium humate, 25 parts of etherified starch, 10 parts of hydroxyethyl cellulose, 7 parts of polyacrylamide, and 6 parts of water-soluble silicone oil; stir under sealing, heat to 120 ° C, and the pressure is 1.0Mpa, constant temperature for 10 hours to obtain semi-finished products; semi-finished products were dried at 100°C, crushed, and added with 10 parts of sulfonated asphalt to compound to obtain fluid loss reducer.
[0040] The synthesis of etherified starch is to take 50 parts of starch, soak in 50 parts of 10% NaOH solution to swell for 24 hours, dry at 75°C, and grind to obtain a semi-finished product; take 30 parts of the semi-finished product, add 30 parts of chloroacetic acid, seal Stir, control the pressure to 1.2Mpa, pH to 7.5, heat to 140°C, and keep the temperature for 16 hours.
[0041] Among the raw materials of the fluid loss control agent, the etherified starch is self-made, and the others are commercial...
Embodiment 2
[0043] Prepared in parts by weight, take 35 parts of sodium humate, 30 parts of etherified starch, 15 parts of hydroxyethyl cellulose, 5 parts of polyacrylamide, and 10 parts of water-soluble silicone oil; stir under sealing, heat to 120 ° C, and the pressure is 1.2Mpa, constant temperature for 8 hours to get a semi-finished product; the semi-finished product was dried at 85°C, crushed, and 7 parts of sulfonated asphalt was added to compound to obtain a fluid loss reducer.
[0044] The synthesis of etherified starch is to take 80 parts of starch, soak in 80 parts of 10% NaOH solution to swell for 28 hours, dry at 85°C, and grind to obtain a semi-finished product; take 50 parts of the semi-finished product, add 50 parts of chloroacetic acid, seal Stir, control the pressure to 1.0Mpa, pH to 7.0, heat to 145°C, and keep the temperature for 17 hours.
[0045] Among the raw materials of the fluid loss control agent, the etherified starch is self-made, and the others are commerciall...
Embodiment 3
[0047] Prepared in parts by weight, take 32 parts of sodium humate, 20 parts of etherified starch, 12 parts of hydroxyethyl cellulose, 10 parts of polyacrylamide, and 5 parts of water-soluble silicone oil; stir under sealing, heat to 120 ° C, and the pressure is 0.8Mpa, constant temperature for 9 hours to get a semi-finished product; the semi-finished product was dried at 90°C, crushed, and 5 parts of sulfonated asphalt was added to compound to get a fluid loss reducer.
[0048] The synthesis of etherified starch is to take 70 parts of starch, soak in 70 parts of 10% NaOH solution to swell for 26 hours, dry at 80°C, and grind to obtain a semi-finished product; take 40 parts of the semi-finished product, add 40 parts of chloroacetic acid, seal Stir, control the pressure to 0.8Mpa, pH to 8.0, heat to 135°C, and keep the temperature for 15 hours.
[0049] Among the raw materials of the fluid loss control agent, the etherified starch is self-made, and the others are commercially ava...
PUM
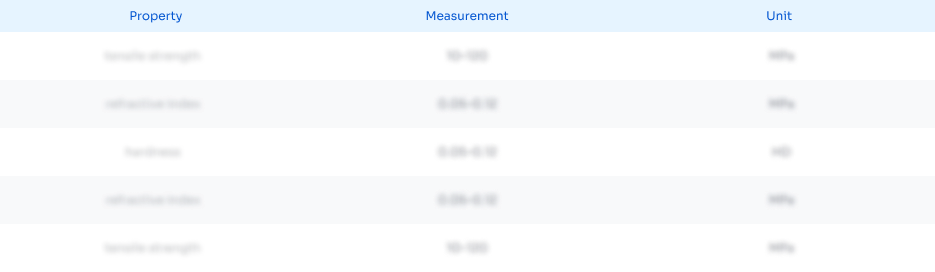
Abstract
Description
Claims
Application Information

- R&D
- Intellectual Property
- Life Sciences
- Materials
- Tech Scout
- Unparalleled Data Quality
- Higher Quality Content
- 60% Fewer Hallucinations
Browse by: Latest US Patents, China's latest patents, Technical Efficacy Thesaurus, Application Domain, Technology Topic, Popular Technical Reports.
© 2025 PatSnap. All rights reserved.Legal|Privacy policy|Modern Slavery Act Transparency Statement|Sitemap|About US| Contact US: help@patsnap.com