Method for preventing surfaces of disc cams from generating gear marks
A disc-shaped cam and tool mark pick-up technology, which is used in grinding machine parts, automatic grinding control devices, metal processing equipment, etc. Improve the textile speed, the error is easier to control, and the effect of eliminating knife marks
- Summary
- Abstract
- Description
- Claims
- Application Information
AI Technical Summary
Problems solved by technology
Method used
Image
Examples
Embodiment 1
[0029] See figure 1 , the method for avoiding the surface of the disc cam to produce the knife mark of the present embodiment comprises the following steps:
[0030] ① The discrete point data of the profile of the disc cam’s parent wheel is measured by the cam precision measuring instrument, and the cam rotation angle signal is obtained by the circular grating encoder of the cam precision measuring instrument, which is obtained by the measuring head and linear grating of the cam precision measuring instrument The displacement signal of the cam lift, and then input the discrete point data of the profile of the measured cam into the computer through the data acquisition card, and in the form of polar coordinates {ρ m , θ m}, where m=1, 2, 3, Λ, k (k=360 / (θ 2 -θ 1 )), ρ m is the mth cam lift data, θ m is the mth sampling angle value, and θ 2 is the second sampling angle value, θ 1 is the first sampling angle value; by (ρ m , θ m ) represents the data of any sampling poin...
Embodiment 2
[0052] In this embodiment, the cam of a certain type is sampled at the angle (ie θ m ) 20 lift data measured from 301 degrees to 320 degrees are processed by the method of embodiment 1 to prevent the cam surface from generating tool marks.
[0053] By step 1. of the method for embodiment 1, measure the discrete point data of the profile of disc cam by cam precision measuring instrument, the lift data of the cam that measures is as shown in table 1 (unit is millimeter), here only selects A section of the area where more knife marks appear. Each sample value is separated by an angle of 1 degree.
[0054] From step ② of the method in Example 1, it can be seen that among these sampling points, the sampling points whose absolute value of the second-order variation is greater than 0.03 are the parts where the knife marks will be generated. From the second-order variation in the fourth column in Table 1 It can be found that 305 degrees, 307 degrees, 310 degrees, 312 degrees, 314 de...
Embodiment 3
[0059] According to step 5. of the method of embodiment 1, by the method for cubic spline interpolation, the data obtained by step 4. of embodiment 2 insert a point at the midpoint of adjacent 2 discrete points and carry out cubic spline interpolation, obtain The data are shown in Table 2 below. It can be seen from Table 2 that the absolute value of the second-order variation of the cam data after cubic spline interpolation does not exceed 0.008, and when the interval angle from the sampling angle is 0.5 degrees, the threshold of the second-order variation of the tool mark will be 0.015 The difference is far, so there is no place where the knife mark will be produced.
[0060] Sampling angle value
PUM
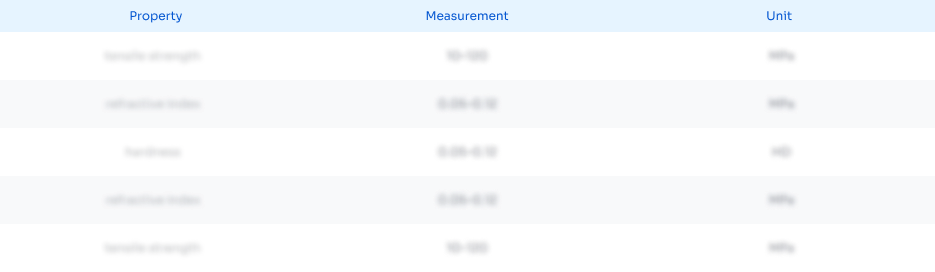
Abstract
Description
Claims
Application Information

- R&D
- Intellectual Property
- Life Sciences
- Materials
- Tech Scout
- Unparalleled Data Quality
- Higher Quality Content
- 60% Fewer Hallucinations
Browse by: Latest US Patents, China's latest patents, Technical Efficacy Thesaurus, Application Domain, Technology Topic, Popular Technical Reports.
© 2025 PatSnap. All rights reserved.Legal|Privacy policy|Modern Slavery Act Transparency Statement|Sitemap|About US| Contact US: help@patsnap.com