One-step spinning and winding combined manufacturing process for 24-head/position multi-heterogeneous hybrid yarn composite fiber
A composite fiber and manufacturing process technology, applied in fiber processing, spinneret assemblies, textiles and papermaking, etc., can solve the problems of production process growth, spinneret heat reduction, melt flow reduction, etc., and achieve product quality The effect of stably improving, reducing melt degradation, and increasing melt flow
- Summary
- Abstract
- Description
- Claims
- Application Information
AI Technical Summary
Problems solved by technology
Method used
Image
Examples
Embodiment
[0032] Embodiment: A spinning and winding joint manufacturing process of 24 ends / position multi-differential mixed fiber composite fibers in one step is carried out according to the following process steps:
[0033] ①. Material preparation: Put the sliced raw materials into the vibrating screening equipment for screening, screen out the powder and particles with inconsistent particle sizes, and obtain the sliced raw materials that meet the requirements, and then transport the sliced raw materials to the silo for standby;
[0034] ②, crystallization and drying: the slices in the silo are sent to the pre-crystallization bed for crystallization, and then the crystallized slices are transported to the slice drying tower for drying to remove the moisture in the slices;
[0035] ③ Melting and filtering: Send the dried slices into the extruder to heat and melt into a melt, and then transport the melt to a melt filter for filtration to remove impurities in the melt;
[0036] ④ M...
PUM
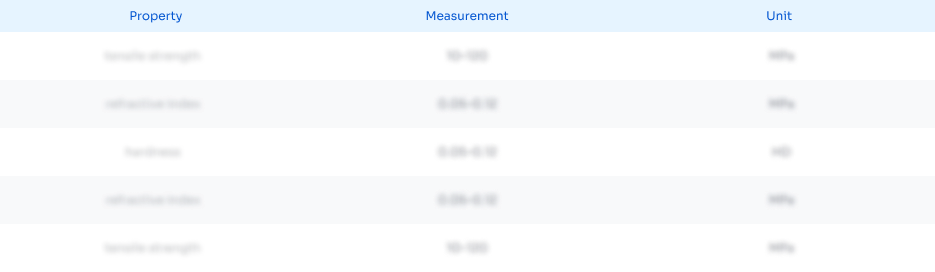
Abstract
Description
Claims
Application Information

- R&D
- Intellectual Property
- Life Sciences
- Materials
- Tech Scout
- Unparalleled Data Quality
- Higher Quality Content
- 60% Fewer Hallucinations
Browse by: Latest US Patents, China's latest patents, Technical Efficacy Thesaurus, Application Domain, Technology Topic, Popular Technical Reports.
© 2025 PatSnap. All rights reserved.Legal|Privacy policy|Modern Slavery Act Transparency Statement|Sitemap|About US| Contact US: help@patsnap.com