Constant displacement quality control method of steel rail flame welding heating and post-weld normalizing
A quality control method, flame welding technology, applied in the direction of comprehensive factory control, comprehensive factory control, electrical program control, etc. The process of detection and control is simple, the operation is convenient, and the effect of strong anti-interference
- Summary
- Abstract
- Description
- Claims
- Application Information
AI Technical Summary
Problems solved by technology
Method used
Image
Examples
Embodiment Construction
[0028] Fig. 1 shows, a kind of embodiment of the present invention is: a kind of constant displacement quality control method of rail flame welding heating and normalizing after welding, and its steps are:
[0029] a. Setting parameters: Obtain the relationship curve between the rail temperature and the longitudinal deformation resistance of the rail through thermal / mechanical simulation tests;
[0030] Figure 2 is the relationship between temperature and longitudinal deformation resistance of U75V rails widely used in railways obtained through thermal / mechanical simulation tests.
[0031] b. Displacement locking: the programmable controller 5 controls the conduction of the solenoid valve 1 on the rod cavity oil circuit of the upsetting oil cylinder 9, and controls the numerical control pump station 10 to feed oil into the rod cavity with the set oil pressure; at the same time, the Connected to the pressure sensor 4 on the rod cavity oil circuit of the upsetting oil cylinder 9...
PUM
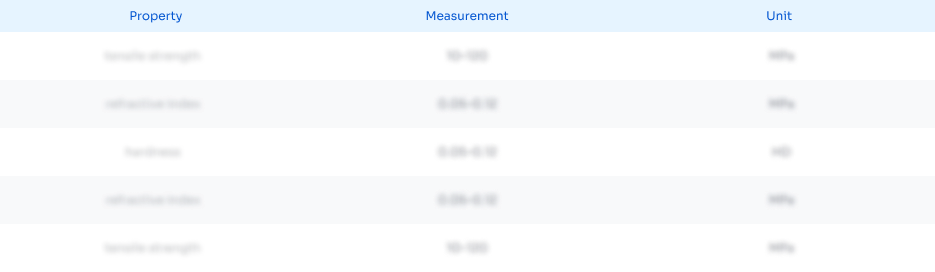
Abstract
Description
Claims
Application Information

- R&D
- Intellectual Property
- Life Sciences
- Materials
- Tech Scout
- Unparalleled Data Quality
- Higher Quality Content
- 60% Fewer Hallucinations
Browse by: Latest US Patents, China's latest patents, Technical Efficacy Thesaurus, Application Domain, Technology Topic, Popular Technical Reports.
© 2025 PatSnap. All rights reserved.Legal|Privacy policy|Modern Slavery Act Transparency Statement|Sitemap|About US| Contact US: help@patsnap.com