Thermal error differential screw compensating device and using method thereof
A technology of compensation device and differential screw, which is applied in other manufacturing equipment/tools, manufacturing tools, etc., can solve the problem of poor robustness and versatility of the compensation control system, error compensation value cannot be inserted in real time, and does not have real-time error compensation function and other problems to achieve the effect of good versatility, smooth movement and simple structure
- Summary
- Abstract
- Description
- Claims
- Application Information
AI Technical Summary
Problems solved by technology
Method used
Image
Examples
Embodiment Construction
[0021] The present invention will be further described below in conjunction with the accompanying drawings and embodiments.
[0022] like figure 1 As shown, a thermal error differential screw compensation device provided by the present invention includes a screw nut transmission system, a worm gear compensation system, a sleeve, a support bearing, a washer, and the like. During the assembly process, the sleeve 5 is first fixed to the machine column with six screws 9 evenly distributed in the circumferential direction, and then the bearings 6, 7, sleeve 3, ball screw nut, and washer 4 are threaded according to the structure shown in the figure. Insert the sleeve 5 and press it tightly. The sleeve 11 uses the washer 8 to press the bearing 7 and connects to the sleeve 5 with six screws 10. The motor direct-coupled reducer base 13 is fixed on the machine tool with four screws 12. The motor The direct-coupled reducer 19 is connected with the worm 14 through the coupling 20, the wo...
PUM
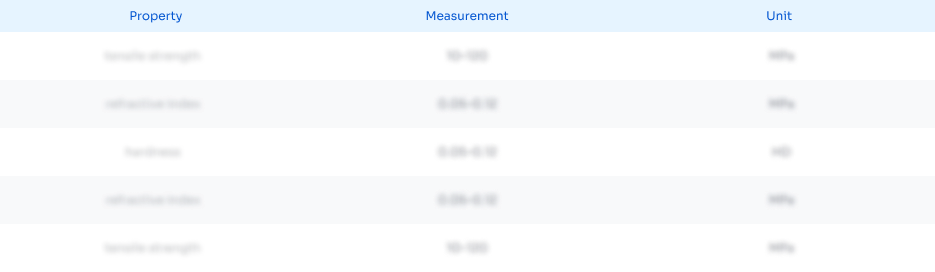
Abstract
Description
Claims
Application Information

- R&D
- Intellectual Property
- Life Sciences
- Materials
- Tech Scout
- Unparalleled Data Quality
- Higher Quality Content
- 60% Fewer Hallucinations
Browse by: Latest US Patents, China's latest patents, Technical Efficacy Thesaurus, Application Domain, Technology Topic, Popular Technical Reports.
© 2025 PatSnap. All rights reserved.Legal|Privacy policy|Modern Slavery Act Transparency Statement|Sitemap|About US| Contact US: help@patsnap.com