Method for removing sulfureted hydrogen from mixture containing iron pentacarbonyl or nickel tetracarbonyl
A technology of nickel tetracarbonyl and iron pentacarbonyl, applied in the field of hydrogen sulfide removal, can solve the problems of harsh production equipment, unsatisfactory iron extraction rate, slow extraction rate and the like
- Summary
- Abstract
- Description
- Claims
- Application Information
AI Technical Summary
Problems solved by technology
Method used
Examples
Embodiment 1
[0012] 7.55g of Cu(NO) 2 ·6H 2 O, 50.5g of Fe(NO 3 ) 3 9H 2 After O is dissolved, loaded on 50.0g γ-Al 2 o 3 Dry at 120°C for 2 hours and set aside. Then weigh 1.0g of CaO and 0.5g of KOH, dissolve them in an appropriate amount of water, and impregnate the same amount into the above-mentioned dried γ-Al 2 o 3 Above, the obtained catalyst was dried at 120°C for 2 hours and calcined at 350°C for 4 hours, and the prepared catalyst was used for future use. Weigh 10g of catalyst and load it into a reaction tube, react at 30°C, and feed CO, iron pentacarbonyl gas-liquid mixture, 1% H 2 S, trace N 2 , trace O 2 , trace H 2 Mixed gas with a small amount of methane, etc., the space velocity is 2000h -1 , to detect H in the outlet gas after passing through the catalyst 2 S content <0.1ppm.
Embodiment 2
[0014] 37.8g of Fe(NO) 3 9H 2 O, 20.6g of Zn(NO 3 ) 2 ·6H 2 After O is dissolved, loaded on 50.0g γ-Al 2 o 3 Dry at 120°C for 2 hours and set aside. Then weigh 1.0g of CaO and 0.5g of KOH, dissolve them in an appropriate amount of water, and impregnate the same amount into the above-mentioned dried γ-Al 2 o 3 Above, the obtained catalyst was dried at 120°C for 2 hours and calcined at 350°C for 4 hours, and the prepared catalyst was used for future use. Weigh 10g of catalyst and load it into a reaction tube, react at 30°C, and feed CO, carbonyl iron gas-liquid mixture, 1.2% H 2 S, trace N 2 , trace O 2 , trace H 2 Mixed gas with a small amount of methane, etc., the space velocity is 2000h -1 , to detect H in the outlet gas after passing through the catalyst 2 S content <0.1ppm.
Embodiment 3
[0016] 50.5g of Fe(NO) 3 9H 2 O, 9.7g of Ni(NO 3 ) 2 ·6H 2 After O is dissolved, loaded on 50.0g γ-Al 2 o 3 Dry at 120°C for 2 hours and set aside. Then weigh 1.0g of CaO and 0.5g of KOH, dissolve them in an appropriate amount of water, and impregnate the same amount into the above-mentioned dried γ-Al 2 o 3 Above, the obtained catalyst was dried at 120°C for 2 hours and calcined at 350°C for 4 hours, and the prepared catalyst was used for future use. Weigh 10g of catalyst and load it into a reaction tube, react at 30°C, and feed CO, carbonyl iron gas-liquid mixture, 2% H 2 S, trace N 2 , trace O 2 , trace H 2 Mixed gas with a small amount of methane, etc., the space velocity is 2000h -1 , to detect H in the outlet gas after passing through the catalyst 2 S content <0.1ppm.
PUM
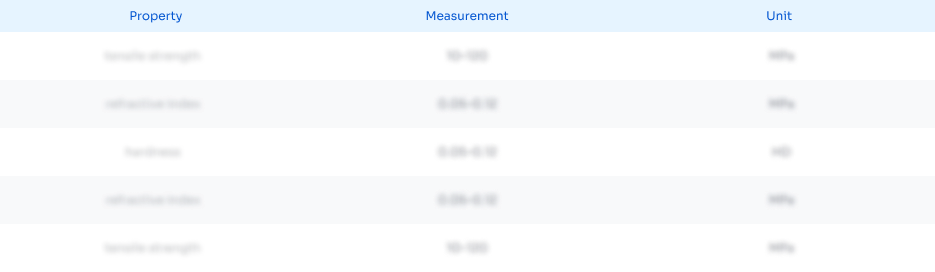
Abstract
Description
Claims
Application Information

- Generate Ideas
- Intellectual Property
- Life Sciences
- Materials
- Tech Scout
- Unparalleled Data Quality
- Higher Quality Content
- 60% Fewer Hallucinations
Browse by: Latest US Patents, China's latest patents, Technical Efficacy Thesaurus, Application Domain, Technology Topic, Popular Technical Reports.
© 2025 PatSnap. All rights reserved.Legal|Privacy policy|Modern Slavery Act Transparency Statement|Sitemap|About US| Contact US: help@patsnap.com