Method for reducing vibration or bending deformation of spindle rotor in high-speed electric spindle
A high-speed electric spindle and spindle rotor technology, applied in the field of mechanical vibration, can solve the problems of unreleased vibration bending deformation, increased spindle bending deformation, increased bearing load, etc., to reduce stress, improve life, and simple structure. Effect
- Summary
- Abstract
- Description
- Claims
- Application Information
AI Technical Summary
Problems solved by technology
Method used
Image
Examples
Embodiment Construction
[0020] to combine figure 1 , the method for reducing the vibration or bending deformation of the main shaft rotor in the high-speed electric spindle of the present invention is to arrange shock absorbing devices with the same structure at the supporting points at both ends of the main shaft rotor 5, the shock absorbing devices include an elastic support ring 2 and a bearing seat 3. Bearings 4 are first installed on the supporting points at both ends of the main shaft rotor 5 and fastened by nuts 6, and then a bearing seat 3 is arranged on the outer diameter of the bearing. The axial width of the bearing seat is ≥ bearing width + nut width + bearing seat rib width , and finally fit the elastic support ring 2 tightly on the outer diameter of the bearing seat, the total width of the elastic support ring = the axial width of the bearing seat, Y-shaped warping wings with equal intervals are arranged radially on the inner cylinder of the elastic support ring, and the The main shaft ...
PUM
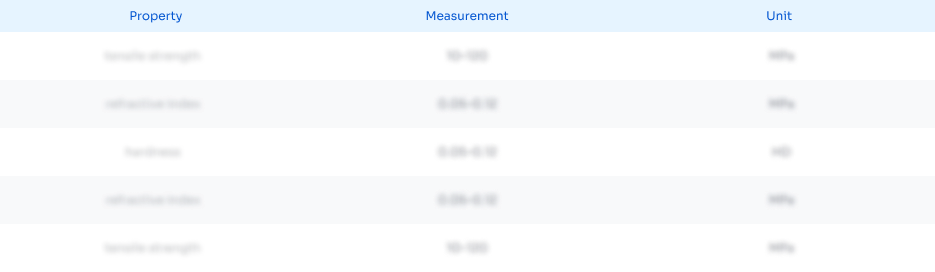
Abstract
Description
Claims
Application Information

- R&D Engineer
- R&D Manager
- IP Professional
- Industry Leading Data Capabilities
- Powerful AI technology
- Patent DNA Extraction
Browse by: Latest US Patents, China's latest patents, Technical Efficacy Thesaurus, Application Domain, Technology Topic, Popular Technical Reports.
© 2024 PatSnap. All rights reserved.Legal|Privacy policy|Modern Slavery Act Transparency Statement|Sitemap|About US| Contact US: help@patsnap.com