Method for mixed selection and re-purification of cassiterite and sulfide ores
A technology of sulfide ore and purification method, applied in chemical instruments and methods, flotation, wet separation, etc., can solve the problems of large proportion of fine particles in tailings, loss of tin, inclusion of tin, etc., to reduce the types of chemicals and effect of quantity
- Summary
- Abstract
- Description
- Claims
- Application Information
AI Technical Summary
Problems solved by technology
Method used
Examples
Embodiment 1
[0019] mineral raw material
[0020] In a tailing mine in Guangxi, the grade of tin in the ore is 0.47%, the grade of lead is 0.43%, the grade of antimony is 0.37%, the grade of zinc is 1.35%, the grade of sulfur is 15.23%, the grade of silicon dioxide is 20.87%, and the grade of calcium carbonate is 4.67%.
[0021] Said cassiterite sulfide ore mixed separation and purification method is carried out as follows:
[0022] 1. According to the stroke rate of the shaker is 19 times / min, and the stroke rate is 255 times / min, the fine-grained cassiterite and sulfide ore with similar specific gravity are enriched into cassiterite sulfide ore mixed coarse concentrate;
[0023] 2. Flotation of cassiterite sulfide ore with coarse concentrate using reverse flotation process to obtain cassiterite coarse concentrate without sulfide ore. The flotation agent used in the reverse flotation process is: water glass 500g / t , sodium sulfide 1000g / t, amyl xanthate 300g / t, 2 # Oil 100g / t.
[0024]...
Embodiment 2
[0032] mineral raw material
[0033] In a tailings mine in Guangxi, the grades of tin in the ore are 0.51%, lead 0.49%, antimony 0.41%, zinc 2.13%, sulfur 16.23%, silicon dioxide 21.65%, and calcium carbonate 5.50%.
[0034] Said cassiterite sulfide ore mixed separation and purification method is carried out as follows:
[0035] 1. According to the stroke rate of the shaker is 21 times / min, and the stroke rate is 265 times / min, the fine-grained cassiterite and sulfide ore with similar specific gravity are enriched into cassiterite sulfide ore mixed coarse concentrate;
[0036] 2. Flotation of cassiterite sulfide ore with coarse concentrate using reverse flotation process to obtain cassiterite coarse concentrate without sulfide ore. The flotation agent used in the reverse flotation process is: water glass 1000g / t , sodium sulfide 2000g / t, amyl xanthate 500g / t, 2 # Oil 120g / t.
[0037] When in use, the medicament is first prepared into the following weight percent concentrati...
Embodiment 3
[0045] mineral raw material
[0046] In a tailing mine in Guangxi, the grade of tin in the ore is 0.48%, the grade of lead is 0.46%, the grade of antimony is 0.39%, the grade of zinc is 1.65%, the grade of sulfur is 15.87%, the grade of silicon dioxide is 19.79%, and the grade of calcium carbonate is 4.93%.
[0047] Said cassiterite sulfide ore mixed separation and purification method is carried out as follows:
[0048] 1. According to the stroke rate of the shaker is 20 times / min, and the stroke rate is 260 times / min, the fine-grained cassiterite and sulfide ore with similar specific gravity are enriched into cassiterite sulfide ore mixed coarse concentrate;
[0049] 2. Use the reverse flotation process to float the sulfide ore by mixing cassiterite sulfide ore with coarse concentrate to obtain cassiterite coarse concentrate without sulfide ore. The flotation agent used in the reverse flotation process is: water glass 800g / t , sodium sulfide 1500g / t, amyl xanthate 400g / t, 2 ...
PUM
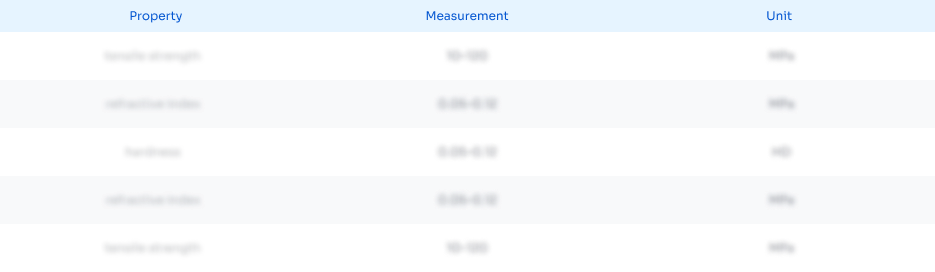
Abstract
Description
Claims
Application Information

- Generate Ideas
- Intellectual Property
- Life Sciences
- Materials
- Tech Scout
- Unparalleled Data Quality
- Higher Quality Content
- 60% Fewer Hallucinations
Browse by: Latest US Patents, China's latest patents, Technical Efficacy Thesaurus, Application Domain, Technology Topic, Popular Technical Reports.
© 2025 PatSnap. All rights reserved.Legal|Privacy policy|Modern Slavery Act Transparency Statement|Sitemap|About US| Contact US: help@patsnap.com