Container reach stacker boom control system and method and container reach stacker
A control system and reachstacker technology, which is applied in the field of container reachstackers and control systems of container reachstacker jib frames, can solve the problems of limited protection of anti-overturning mechanisms, and achieve the effects of preventing overturning, preventing overturning, and reducing complexity
- Summary
- Abstract
- Description
- Claims
- Application Information
AI Technical Summary
Problems solved by technology
Method used
Image
Examples
Embodiment Construction
[0021] figure 1 It is a schematic diagram of the control system of the container front boom jib according to the present invention, wherein the first detection part 1 and the second detection part 2 are connected with the controller 4 through the CAN data bus, wherein the first detection part 1 is used for Detect the elongation and elevation angle of the boom 3; the second detection component 2 is used to detect the pressure of the left and right pitch cylinders 5, 6 of the boom 3. The controller 4 receives these parameters, and calculates the stabilizing moment and the overturning moment at the current position, thereby determining the moment percentage. Wherein, when the moment percentage is lower than the critical predetermined value, the controller 4 judges that the jib 3 is in a safe area, and the safety buffer The coefficient is 1; when the torque percentage is higher than the critical predetermined value, the controller 4 judges that the boom 3 is in a dangerous area, a...
PUM
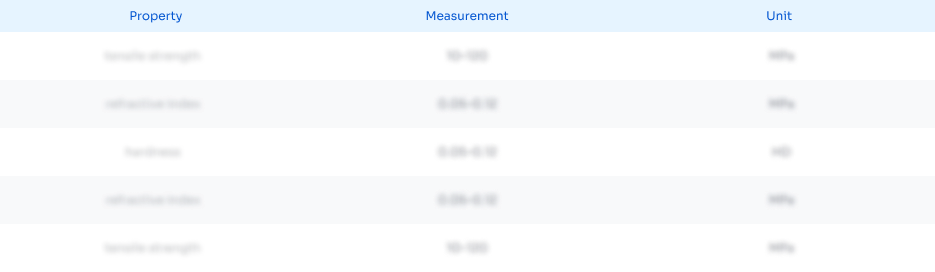
Abstract
Description
Claims
Application Information

- R&D
- Intellectual Property
- Life Sciences
- Materials
- Tech Scout
- Unparalleled Data Quality
- Higher Quality Content
- 60% Fewer Hallucinations
Browse by: Latest US Patents, China's latest patents, Technical Efficacy Thesaurus, Application Domain, Technology Topic, Popular Technical Reports.
© 2025 PatSnap. All rights reserved.Legal|Privacy policy|Modern Slavery Act Transparency Statement|Sitemap|About US| Contact US: help@patsnap.com