Shearing stress detection-based quartz micromechanical gyro with criss-cross structure
A technology of micro-mechanical gyroscope and cross, which is applied in the measurement of the force of the piezoelectric device, the speed measurement of the gyro effect, the gyroscope/steering sensing equipment, etc., which can solve the problem of improving the sensitivity of the unfavorable micro-mechanical gyroscope and reducing vibration. Problems such as quality factor and gyro performance are greatly affected, and the effects of improving the structure's anti-interference ability, improving the structure's sensitivity, and novel structure
- Summary
- Abstract
- Description
- Claims
- Application Information
AI Technical Summary
Problems solved by technology
Method used
Image
Examples
Embodiment 1
[0022] Embodiment 1: as figure 1 , figure 2 with image 3 As shown, the present invention is based on the cross-structure quartz micromechanical gyroscope for shear stress detection, including a substrate 1 and a gyroscope assembly connected together by bonding, and the gyroscope assembly includes a detection beam 3, more than one driving beam 4, The detection electrode and the driving electrode, the driving beam 4 and the detection beam 3 are arranged in a cross shape, the two ends of the driving beam 4 are provided with movable masses, the driving electrodes are installed on the outer surface of the driving beam 4, and the detection electrodes are installed on the outer surface of the driving beam 4. The outer surface of the beam 3 is detected. Both ends of the detection beam 3 are connected to a supporting frame 2 , and the driving beam 4 is located in the supporting frame 2 . The length direction of the driving beam 4 is along the Y crystal direction of the quartz, the...
Embodiment 2
[0029] Embodiment 2: as Figure 4As shown, the structure of this embodiment is basically the same as that of Embodiment 1, the difference being that: the two ends of the detection beam 3 are respectively connected with a supporting mass 23 to replace the supporting frame 2 . The working principle of this embodiment is the same as that of Embodiment 1, and will not be repeated here.
Embodiment 3
[0030] Embodiment 3: as Figure 5 As shown, the structure of this embodiment is basically the same as that of Embodiment 1, and the difference is that more than one opening 24 is opened on the detection beam 3 to reduce the internal stress of the detection beam 3 . The working principle of this embodiment is the same as that of Embodiment 1, and will not be repeated here.
PUM
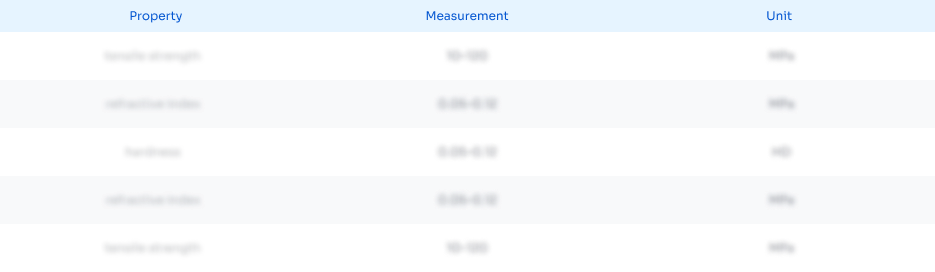
Abstract
Description
Claims
Application Information

- R&D
- Intellectual Property
- Life Sciences
- Materials
- Tech Scout
- Unparalleled Data Quality
- Higher Quality Content
- 60% Fewer Hallucinations
Browse by: Latest US Patents, China's latest patents, Technical Efficacy Thesaurus, Application Domain, Technology Topic, Popular Technical Reports.
© 2025 PatSnap. All rights reserved.Legal|Privacy policy|Modern Slavery Act Transparency Statement|Sitemap|About US| Contact US: help@patsnap.com