Segmental slipping and assembling process of overhead large-span steel structure
A steel structure, large-span technology, applied in the direction of building structure, construction, building materials processing, etc., to achieve the effect of high installation precision, scientific and effective construction method, and fast construction speed
- Summary
- Abstract
- Description
- Claims
- Application Information
AI Technical Summary
Problems solved by technology
Method used
Examples
Embodiment 1
[0060] The second phase of Jindu Han Palace is located at No. 66 Linjiang Avenue, Wuhan, with a 32-story frame shear wall structure. It started construction on December 15, 2006. The total construction area is 62112.14 square meters, the basement construction area is 7871.96 square meters, and the top floor is a large-span exhibition hall. The roof truss structure above the exhibition hall is a large-span and high-section steel pipe truss structure, with a total of 12 brackets, 10 main trusses, 68 secondary trusses, a large number of horizontal supports and purlins, with a total weight of 2700t. Among them, the span of the bracket is 36m, the span of the main truss is 60m, and the span of the secondary truss is 12m, which are evenly arranged along the length direction of the main truss at a distance of 6m. The main truss is undulating, with a height of 4-9m. It is in the shape of a two-way broken line, with a large diameter, complex nodes, and multiple intersecting steel pipes....
Embodiment 2
[0063] Three Gold One Hong Kong Image Project, the project is located in West Gutian Road, Wuhan City, 18-story frame shear wall structure, the third floor is the steel structure truss of the transfer floor, four reinforced concrete cylinders at the four corners are used as giant frame columns, and the steel structure truss The largest size is 16.2mX5.6m (length X height), the heaviest up to 22.3 tons. Also adopt the method described in embodiment 1 to install, ensure the quality and safety of construction, and this construction method saves construction measures cost about 150,000 in total, and the total construction period is advanced 30 days.
Embodiment 3
[0065] The aerospace capital residential building project is located in Dongfang Development Zone, Xiaogan City, Hubei Province. Construction started on November 8, 2008. The total construction area is 19,029 square meters, the basement area is 1,450 square meters, the 18-story frame shear wall structure, and the three-story transfer floor hall is a steel structure truss structure. The high-altitude and large-span steel structure segmented push-slide assembly method adopted in this project ensures the quality and safety of the construction, and this construction method saves a total of about 200,000 construction measures and the total construction period is advanced by 60 days.
PUM
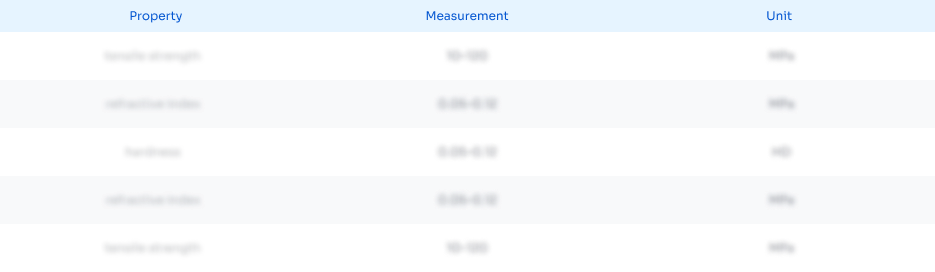
Abstract
Description
Claims
Application Information

- Generate Ideas
- Intellectual Property
- Life Sciences
- Materials
- Tech Scout
- Unparalleled Data Quality
- Higher Quality Content
- 60% Fewer Hallucinations
Browse by: Latest US Patents, China's latest patents, Technical Efficacy Thesaurus, Application Domain, Technology Topic, Popular Technical Reports.
© 2025 PatSnap. All rights reserved.Legal|Privacy policy|Modern Slavery Act Transparency Statement|Sitemap|About US| Contact US: help@patsnap.com