Sintering method of high-Ti type V-Ti magnetite concentrate
A technology of vanadium-titanium magnetite concentrate and sintering method, which is applied in the field of sintering of high-titanium vanadium-titanium magnetite concentrate, and can solve the problems of unreported test and production data, etc.
- Summary
- Abstract
- Description
- Claims
- Application Information
AI Technical Summary
Problems solved by technology
Method used
Examples
Embodiment 1
[0043] Medium-titanium type vanadium-titanium magnetite concentrate is added with 5%, the proportion of rich ore is 28%, the proportion of returned ore is 35%, the proportion of quicklime is 5%, the proportion of limestone is 7.7%, and the proportion of coke powder is 4.8%. Sintering basicity control is 2.35 times (CaO / SiO in sinter 2 Ratio), the ratio of quicklime digestion water is 2:1, the water content of the sintering mixture is 7.3±0.1wt%, and the material is lightly compacted.
[0044] The results show that, compared with the baseline period, the proportion of sinter mixture particle size > 3mm is 57%, the content of calcium ferrite in sintered ore increases by 1.5 percentage points, the drum strength of sintered ore increases by 0.5 percentage points, and the yield increases by 0.75 percentage points. Yield increased by 0.8%.
Embodiment 2
[0046] Medium-titanium type vanadium-titanium magnetite concentrate is added with 7.5%, the ratio of rich ore is 28%, the ratio of returned ore is 37%, the ratio of quicklime is 6%, the ratio of limestone is 6.3%, and the ratio of coke powder is 4.85%. The sintering alkalinity is 2.35, the ratio of quicklime digestion water is 2:1, the water content of the sintering mixture is 7.3%, and the material is lightly compacted.
[0047] The results show that, compared with the base period, the proportion of sinter mixture particle size > 3mm is 61%, the calcium ferrite content in sintered ore increases by 1.75 percentage points, the drum strength of sintered ore increases by 0.5 percentage points, and the finished product rate increases by 1.8 percentage points. Yield increased by 2.0%.
Embodiment 3
[0049] Medium-titanium type vanadium-titanium magnetite concentrate is added by 10%, the ratio of rich ore is 28%, the ratio of returned ore is 39%, the ratio of quicklime is 7%, the ratio of limestone is 5%, and the ratio of coke powder is 4.9%. The sintering alkalinity is 2.35, the ratio of quicklime digestion water is 2:1, the water content of the sintering mixture is 7.3+0.1%, and the material is lightly compacted.
[0050] The results show that, compared with the base period, the proportion of sinter mixture particle size > 3mm is 67%, the content of calcium ferrite in sintered ore increases by 2 percentage points, the drum strength of sintered ore increases by 0.8 percentage points, and the finished product rate increases by 2.3 percentage points. Yield increased by 3.0%.
PUM
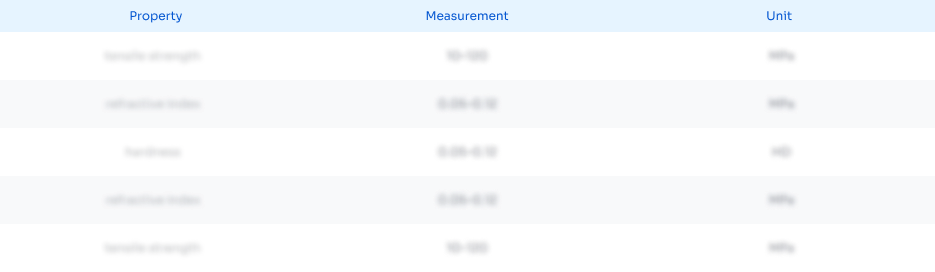
Abstract
Description
Claims
Application Information

- Generate Ideas
- Intellectual Property
- Life Sciences
- Materials
- Tech Scout
- Unparalleled Data Quality
- Higher Quality Content
- 60% Fewer Hallucinations
Browse by: Latest US Patents, China's latest patents, Technical Efficacy Thesaurus, Application Domain, Technology Topic, Popular Technical Reports.
© 2025 PatSnap. All rights reserved.Legal|Privacy policy|Modern Slavery Act Transparency Statement|Sitemap|About US| Contact US: help@patsnap.com