Parameter setting and reeling method of thermal tandem rolling stainless steel band reeling equipment
A technology for stainless steel strips and coiling equipment, which is applied in the parameter setting of hot continuous rolling stainless steel strip coiling equipment and the field of coiling, can solve the problems of unstable incoming material width, easy edge folding, and low qualification rate. , to achieve the effect of reducing the number of times of coiling scrap
- Summary
- Abstract
- Description
- Claims
- Application Information
AI Technical Summary
Problems solved by technology
Method used
Examples
Embodiment 1
[0121] After the above settings are made to the equipment, 304 stainless steel with a thickness d of 3.0mm can be coiled. This embodiment includes the following steps in sequence:
[0122] a delivery
[0123] a. When the steel strip head passes through six sets of roller tables at a speed of 9m per second from the last stand of the finishing mill, the first group of roller tables, the second group of roller tables, the third group of roller tables, the fourth group of roller tables, and the fifth group of roller tables The advanced conveying speeds of the road and the sixth group of roller tables (the speed exceeding the last stand of the finishing mill) are 11.07m, 11.16m, 11.34m, 11.61m, 11.79m and 11.97m rotations per second respectively.
[0124] b When the steel belt passes through the side guide plate, the pressure coefficient of the side guide plate: 0.5~0.8, and the added value of the side guide plate is 0~+15mm.
[0125] c When the steel strip head passes through th...
Embodiment 2
[0145] In this embodiment, Ni-based stainless steel 304 is coiled, the thickness d is 6.0mm, and the width is 1250mm. The coiling step is the same as that of Example 1.
[0146] The above four embodiments are applicable to Ni-based stainless steels 321, 316 and 316L. The setting of coiling parameters and coiling steps are the same as those of 304 with the same thickness.
Embodiment 3
[0150] In this embodiment, Cr-based stainless steel 430 is coiled, the thickness d is 3.0 mm, and the width is 1250 mm. The coiling step is the same as that of Example 1.
[0151] The third embodiment of setting parameters and the steel strip coiling embodiment three are applicable to Cr-based stainless steel 436, 443 and 409, and the setting of coiling parameters and coiling steps are the same as those of 430 with the same thickness.
[0152] In this application document:
[0153] The percentage of total lead rate and lag rate is a percentage value determined based on the rolling speed of the last stand of finish rolling.
[0154] The total advance rate of the roller table is the percentage of the linear speed when the roller table rotates before coiling, that is, the advanced conveying speed, to the rolling speed of the final stand of the finish rolling.
[0155] The hysteresis rate of the roller table is the percentage of the linear speed when the roller table rotates dur...
PUM
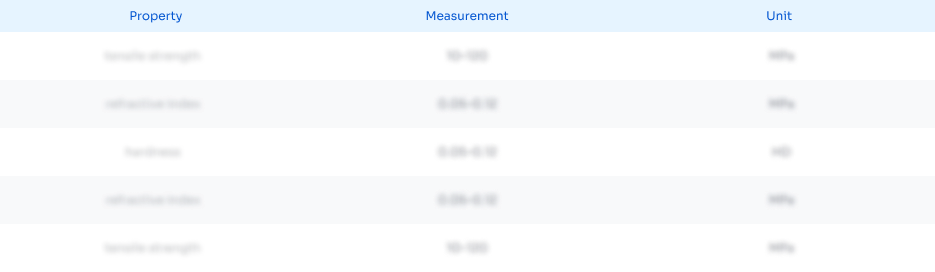
Abstract
Description
Claims
Application Information

- R&D
- Intellectual Property
- Life Sciences
- Materials
- Tech Scout
- Unparalleled Data Quality
- Higher Quality Content
- 60% Fewer Hallucinations
Browse by: Latest US Patents, China's latest patents, Technical Efficacy Thesaurus, Application Domain, Technology Topic, Popular Technical Reports.
© 2025 PatSnap. All rights reserved.Legal|Privacy policy|Modern Slavery Act Transparency Statement|Sitemap|About US| Contact US: help@patsnap.com