Process for after-finishing biological enzymes of ramie yarn and bast fiber cloth
A post-finishing and biological enzyme technology, applied in the direction of biochemical fiber treatment, fiber treatment, plant fiber, etc., can solve the problems of large fiber strength damage, easy nozzle blockage, poor softening effect, etc., to improve product quality and reduce production costs. , The time-saving effect of the process
- Summary
- Abstract
- Description
- Claims
- Application Information
AI Technical Summary
Problems solved by technology
Method used
Examples
Embodiment 1
[0019] A bio-enzyme post-finishing process for hemp yarn and hemp-like fabrics, using an overflow dyeing machine with a bath ratio of 1:6 for bio-enzyme post-finishing treatment:
[0020] (1) Low-temperature neutral compound enzyme singeing: put the compound enzyme ingredients in the material tank, turn on the stirring device to mix the compound enzyme ingredients evenly, control the pH value of the compound enzyme ingredients to 6.5, and then heat up to 50°C to obtain a solution, Utilize a stretcher with a lower width of 160cm, control the overfeed amount to 1%, and the cloth speed to 90m / min, put the to-be-processed hemp yarn and hemp cloth into the solution, keep the cloth below the liquid level, and keep warm for 30 minutes;
[0021] (2) Softening with low-temperature neutral compound enzyme: put the soft ingredients in the material tank, turn on the stirring device to mix the soft ingredients evenly, control the pH value of the soft ingredients to 6.5, then introduce the s...
Embodiment 2
[0026] A bio-enzyme post-finishing process for hemp yarn and hemp-like fabrics, using a continuous long-vehicle production line for bio-enzyme post-finishing treatment:
[0027] (1) Low-temperature neutral compound enzyme singeing: add the compound enzyme ingredients in the automatic feeder, then add the compound enzyme ingredients into the two tanks, control the pH of the compound enzyme ingredients to be 8.0, and then heat up to 60°C to obtain solution, using a stretcher with a lower frame width of 170cm, controlling the overfeed amount to 3%, and the cloth speed to 110m / min, put the hemp yarn and hemp cloth to be processed into the solution, keep the cloth below the liquid level, and keep warm 60min;
[0028] (2) Softening with low-temperature neutral compound enzyme: add soft ingredients into the automatic feeding device, then add the soft ingredients into two tanks, control the pH value of the soft ingredients to 8.0, and then raise the temperature to 60°C to obtain a sol...
Embodiment 3
[0032] A bio-enzyme post-finishing process for hemp yarn and hemp-like fabrics, using a continuous long-vehicle production line for bio-enzyme post-finishing treatment:
[0033] (1) Low-temperature neutral compound enzyme singeing: add compound enzyme ingredients into the tank of the long car production line, then add the compound enzyme ingredients into the two tanks, control the pH value of the ingredients to 7.0, and then raise the temperature to 50°C to obtain a solution , using a stretcher with a lower frame width of 165cm, control the overfeeding amount to 2%, and the cloth speed to 100m / min, put the to-be-processed hemp yarn and hemp cloth into the solution, keep the cloth below the liquid level, and keep it warm for 40 minutes ;
[0034] (2) Softening with low-temperature neutral compound enzyme: add soft ingredients into the automatic feeding device, then add the soft ingredients into the two tanks, control the pH value of the soft ingredients to 7.0, and then raise t...
PUM
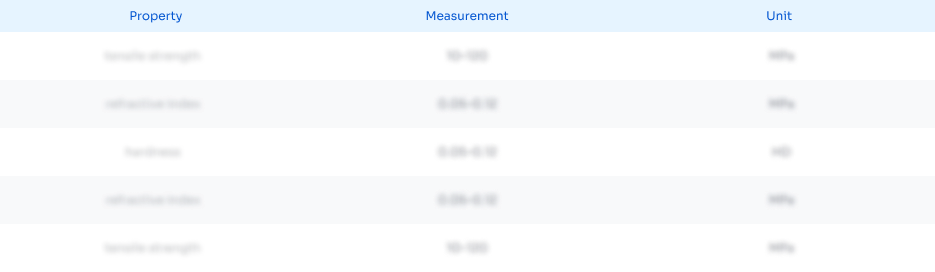
Abstract
Description
Claims
Application Information

- R&D
- Intellectual Property
- Life Sciences
- Materials
- Tech Scout
- Unparalleled Data Quality
- Higher Quality Content
- 60% Fewer Hallucinations
Browse by: Latest US Patents, China's latest patents, Technical Efficacy Thesaurus, Application Domain, Technology Topic, Popular Technical Reports.
© 2025 PatSnap. All rights reserved.Legal|Privacy policy|Modern Slavery Act Transparency Statement|Sitemap|About US| Contact US: help@patsnap.com