Flame retardant glass fiber mesh
A technology of flame-retardant glass fiber and flame-retardant glue, which is applied in fiber processing, textiles and papermaking, etc., can solve the problems of high cost, pollute the environment, and cannot meet the needs of market competition, etc., and achieve good flame-retardant performance and low raw material cost , The effect of convenient operation and control
- Summary
- Abstract
- Description
- Claims
- Application Information
AI Technical Summary
Problems solved by technology
Method used
Examples
Embodiment 1
[0012] 70 parts of vinylidene chloride polymer emulsion, 28 parts of pure acrylic emulsion, 1.8 parts of nano-silica, 2 parts of antimony trioxide, 0.04 part of sodium polyacrylate dispersant, mix well in the presence of appropriate amount of water, and coat the mixture Dry the liquid glass fiber cloth in an oven at 105°C for about 90 seconds until the glue is completely dry, then remove it from the oven. The obtained mesh cannot be ignited with fire, the warp and weft are positioned well, the hand feels non-sticky and elastic, and the appearance is similar to ordinary glass fiber mesh without yellowing.
Embodiment 2
[0014] 70 parts of vinylidene chloride polymer emulsion, 37 parts of styrene-acrylic emulsion, 2.2 parts of nanoclay, 2.3 parts of antimony trioxide, 0.075 parts of sodium polyacrylate dispersant, mix well in the presence of an appropriate amount of water, and apply the mixture liquid Dry the glass fiber cloth in an oven at 115°C for about 90 seconds until the glue is completely dry, then remove it from the oven. The obtained mesh cannot be ignited with fire, the warp and weft are positioned well, the hand feels non-sticky and elastic, and the appearance is similar to ordinary glass fiber mesh without yellowing.
Embodiment 3
[0016] 70 parts of vinylidene chloride polymer emulsion, 32 parts of styrene-butadiene emulsion, 4.6 parts of nanoclay, 2.3 parts of antimony trioxide, 0.045 parts of sodium alkylnaphthalene sulfonate dispersant, mix well in the presence of appropriate amount of water, and coat the Dry the glass fiber cloth of the mixture liquid in an oven at 110°C for about 85 seconds until the glue is completely dry, then remove it from the oven. The obtained mesh cannot be ignited with fire, the warp and weft are positioned well, the hand feels non-sticky and elastic, and the appearance is similar to ordinary glass fiber mesh without yellowing.
PUM
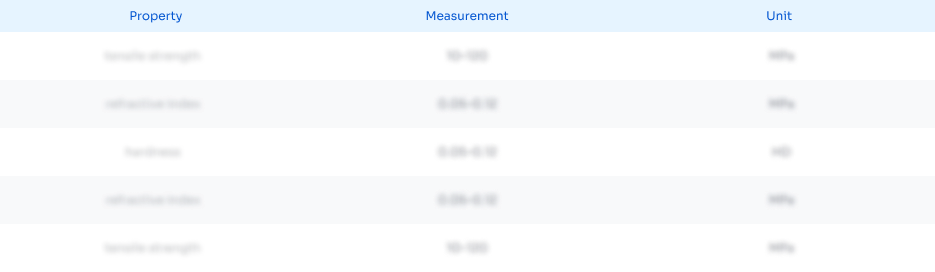
Abstract
Description
Claims
Application Information

- R&D
- Intellectual Property
- Life Sciences
- Materials
- Tech Scout
- Unparalleled Data Quality
- Higher Quality Content
- 60% Fewer Hallucinations
Browse by: Latest US Patents, China's latest patents, Technical Efficacy Thesaurus, Application Domain, Technology Topic, Popular Technical Reports.
© 2025 PatSnap. All rights reserved.Legal|Privacy policy|Modern Slavery Act Transparency Statement|Sitemap|About US| Contact US: help@patsnap.com