Hot runner carbon fiber direct-shaping technique of vanes of wind driven generator
A technology of wind power generator and molding process, applied in the direction of coating, etc., can solve problems such as difficulties, uneven glue content, incomplete curing, etc., and achieve an increase in input-output ratio, high energy conversion rate, and reduced maintenance costs Effect
- Summary
- Abstract
- Description
- Claims
- Application Information
AI Technical Summary
Problems solved by technology
Method used
Examples
Embodiment 1
[0024] Example 1: A hot runner carbon fiber direct molding process for wind turbine blades
[0025] A hot-runner carbon fiber direct molding process for wind turbine blades. To form a 2-meter-long wind turbine blade, 5 kilograms of raw materials are required for one piece of material. The raw material formula is as follows: 3.4 kilograms of nylon 6 (the brand is nylon 1013B), 1.6 kilograms of carbon fiber . After the concave mold and the convex mold are closed, the flow rate is controlled by a PC (computer). After the nylon 6 in the raw material is melted in the hot runner, the carbon fiber is driven into the mold cavity from five nozzles; the five nozzles are along the length direction of the mold cavity. Arranged, the temperature of raw materials passing through each nozzle from the tip of the corresponding wind turbine blade to the root of the blade is as follows: 211°C~213°C, 216°C~218°C, 220°C~221°C, 224°C~226°C, 229°C ~231°C. Then hold the mold for about 32 seconds to ...
Embodiment 2
[0026] Example 2: A hot runner carbon fiber direct molding process for wind turbine blades
[0027] A hot-runner carbon fiber direct molding process for wind turbine blades. To form a 2-meter-long wind turbine blade, 5 kilograms of raw materials are required for one piece of material. The raw material formula is as follows: 3.45 kilograms of nylon 6 (the brand is nylon 1013B), 1.5 kilograms of carbon fiber , 0.05 kg of toner. After the concave mold and the convex mold are closed, the flow rate is controlled by a PC (computer). After the nylon 6 in the raw material is melted in the hot runner, the carbon fiber is driven into the mold cavity from 10 nozzles; the 10 nozzles are along the length direction of the mold cavity. Arranged, the temperature of raw materials passing through each nozzle from the tip of the corresponding wind turbine blade to the root of the blade is as follows: 212°C, 215°C, 218°C, 221°C, 224°C, 227°C, 230°C, 232°C, 234°C , 236°C. Then hold the mold for ...
PUM
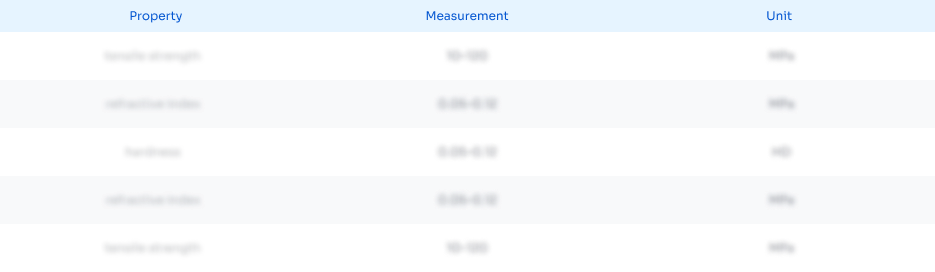
Abstract
Description
Claims
Application Information

- Generate Ideas
- Intellectual Property
- Life Sciences
- Materials
- Tech Scout
- Unparalleled Data Quality
- Higher Quality Content
- 60% Fewer Hallucinations
Browse by: Latest US Patents, China's latest patents, Technical Efficacy Thesaurus, Application Domain, Technology Topic, Popular Technical Reports.
© 2025 PatSnap. All rights reserved.Legal|Privacy policy|Modern Slavery Act Transparency Statement|Sitemap|About US| Contact US: help@patsnap.com