Multiphase permanent magnet fault-tolerant motor control system in half-bridge structure
A technology for permanent magnet fault tolerance and motor control, applied in control systems, AC motor control, electrical components, etc., can solve problems such as multi-power devices, affecting system reliability, and increased volume and weight, and achieve small size and excellent drive performance , The effect of low system cost
- Summary
- Abstract
- Description
- Claims
- Application Information
AI Technical Summary
Problems solved by technology
Method used
Image
Examples
Embodiment Construction
[0017] specific implementation plan
[0018] The present invention will be further described below in conjunction with the accompanying drawings and specific embodiments.
[0019] The invention patent is aimed at the M-phase permanent magnet fault-tolerant motor control system, the circuit topology is as follows image 3 Connection shown.
[0020] Inverter faults mainly include short-circuit faults of power switching devices, open-circuit faults of power switching devices, short-circuit faults at the end of motor windings, and open-circuit faults of windings. When the motor system runs without fault, it is M-phase symmetrical operation. When either phase, to A
[0021] 1. The power switching device is short-circuited. Once a fault occurs, the PTC resistor R 1 The current on the circuit will increase sharply, the PTC resistor will heat up, the temperature will rise sharply, and it will show a high resistance state. The characteristics are as follows: Figure 4 As shown, t...
PUM
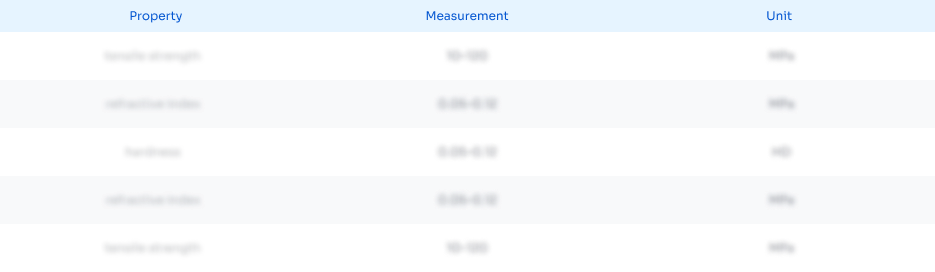
Abstract
Description
Claims
Application Information

- Generate Ideas
- Intellectual Property
- Life Sciences
- Materials
- Tech Scout
- Unparalleled Data Quality
- Higher Quality Content
- 60% Fewer Hallucinations
Browse by: Latest US Patents, China's latest patents, Technical Efficacy Thesaurus, Application Domain, Technology Topic, Popular Technical Reports.
© 2025 PatSnap. All rights reserved.Legal|Privacy policy|Modern Slavery Act Transparency Statement|Sitemap|About US| Contact US: help@patsnap.com