Manufacturing technique of reinforced concrete drain pipe
A technology of reinforced concrete and manufacturing process, applied in manufacturing tools, reinforcing molding, ceramic molding machines, etc., can solve the problems of collapse of drainage pipes, complex structure, low output, etc. Effect
- Summary
- Abstract
- Description
- Claims
- Application Information
AI Technical Summary
Problems solved by technology
Method used
Image
Examples
Embodiment Construction
[0017] The manufacturing process steps of this kind of reinforced concrete drainpipe among the present invention are: first make steel bar skeleton 4 according to the size of reinforced concrete drainpipe, and make F steel ring 1, described steel bar skeleton 4 is double-layer skeleton, and in steel bar skeleton 4 is provided with inner and outer top hooks, and the top hooks are evenly distributed on the steel frame; then the F steel ring 1 is placed on the bottom mold 2, and the top hook on the steel frame 4 is welded to the F steel ring 1 , so that the steel frame 4 is fixedly connected with the F steel ring 1; then the bottom form 2 and the steel frame 4 are inserted into the outer form 5, and the outer form 5 is connected with the bottom form 2; then the outer form 5 is placed in the pool pit outside the inner film 6 of the outer mold 5, and install the socket mold 7 on the upper end surface of the outer mold 5, the socket mold 7 matches the F steel ring 1, that is, the upp...
PUM
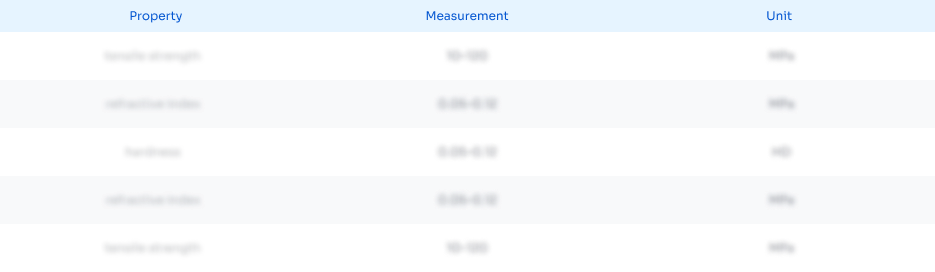
Abstract
Description
Claims
Application Information

- R&D
- Intellectual Property
- Life Sciences
- Materials
- Tech Scout
- Unparalleled Data Quality
- Higher Quality Content
- 60% Fewer Hallucinations
Browse by: Latest US Patents, China's latest patents, Technical Efficacy Thesaurus, Application Domain, Technology Topic, Popular Technical Reports.
© 2025 PatSnap. All rights reserved.Legal|Privacy policy|Modern Slavery Act Transparency Statement|Sitemap|About US| Contact US: help@patsnap.com