Radiating structure and molding method thereof
A technology of heat dissipation structure and molding method, which is applied in the cooling of instruments, parts of instruments, instruments, etc., can solve the problems of large processing time, inconsistent production rate, and difficulty in further enhancing the cooling effect of cooling airflow, so as to improve the The effect of air cooling efficiency
- Summary
- Abstract
- Description
- Claims
- Application Information
AI Technical Summary
Problems solved by technology
Method used
Image
Examples
Embodiment Construction
[0029] refer to figure 2 , image 3 ,and Figure 4 As shown, it is a heat dissipation structure 100 disclosed in the first embodiment of the present invention, which includes an extruded part 110 and a plurality of fins 120. The extruded part 110 and the fins 120 are integrally formed, and the cooling air can pass through The shape part 110 improves the air cooling effect.
[0030] Figure 5A for image 3 and Figure 4 Schematic cross-section along A-A'. The extruded part 110 is a single piece made by extrusion process, or a tubular structure formed around the plate. The extruded part 110 has a plurality of bending parts 111 and a plurality of connecting parts 112 extending along a long axis direction alternately. The connecting portion 112 is used for connecting adjacent bent portions 111 , and the bent portion 111 protrudes from the surface of the extruded part 110 . Due to the characteristics of the extrusion process, the bent portions 111 extend along the long axi...
PUM
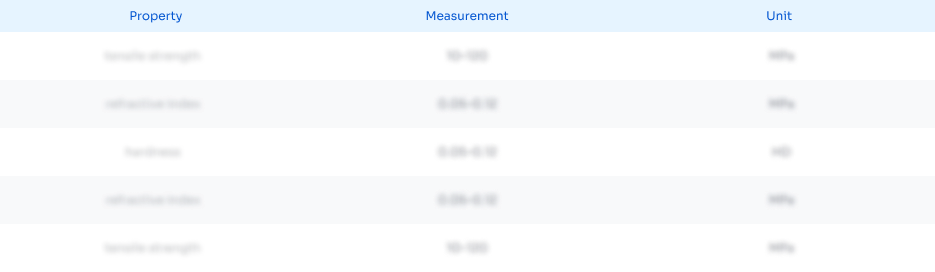
Abstract
Description
Claims
Application Information

- R&D
- Intellectual Property
- Life Sciences
- Materials
- Tech Scout
- Unparalleled Data Quality
- Higher Quality Content
- 60% Fewer Hallucinations
Browse by: Latest US Patents, China's latest patents, Technical Efficacy Thesaurus, Application Domain, Technology Topic, Popular Technical Reports.
© 2025 PatSnap. All rights reserved.Legal|Privacy policy|Modern Slavery Act Transparency Statement|Sitemap|About US| Contact US: help@patsnap.com