Axial load resistant no-return-difference torque output ball-hinged driving mechanism
An axial load and drive mechanism technology, applied in electromechanical devices, electric components, control of mechanical energy, etc., can solve the problems of poor axial load resistance, large transmission clearance, axial length and dimension changes, etc., to achieve axial load resistance. Good performance, good transmission rigidity, good effect without backlash
- Summary
- Abstract
- Description
- Claims
- Application Information
AI Technical Summary
Problems solved by technology
Method used
Image
Examples
Embodiment Construction
[0032] The present invention will be further described in detail below in conjunction with the accompanying drawings.
[0033] Please see figure 1 , Figure 1A As shown, an axial load-resistant non-backlash torque output spherical joint drive mechanism of the present invention includes a servo DC motor 1, a motor shaft coupling block 2, a cross slider 3, a ball joint outer ring 4, and an output shaft 5. Motor fastening screw 6, motor mounting seat 7, blank holder ring fastening screw 8, blank holder ring 9, ball joint inner ring 10, first angular contact ball bearing 11, second angular contact ball bearing 12, bearing Outer retaining ring 13, output shaft fastening nut 14.
[0034] Wherein, the drive unit is composed of a servo DC motor 1 , a motor shaft coupling block 2 , a motor fastening screw 6 and a motor mount 7 .
[0035] Wherein, the transmission unit is composed of the motor shaft coupling block 2, the cross slide block 3 and the output shaft 5.
[0036] Wherein, ...
PUM
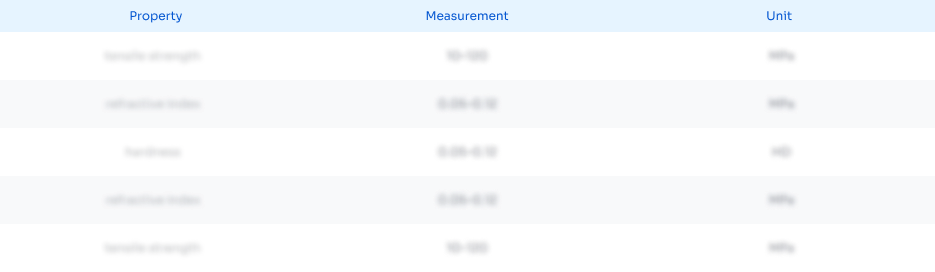
Abstract
Description
Claims
Application Information

- R&D
- Intellectual Property
- Life Sciences
- Materials
- Tech Scout
- Unparalleled Data Quality
- Higher Quality Content
- 60% Fewer Hallucinations
Browse by: Latest US Patents, China's latest patents, Technical Efficacy Thesaurus, Application Domain, Technology Topic, Popular Technical Reports.
© 2025 PatSnap. All rights reserved.Legal|Privacy policy|Modern Slavery Act Transparency Statement|Sitemap|About US| Contact US: help@patsnap.com