Triaxial acceleration sensor
An acceleration sensor, axis technology, applied in the measurement of acceleration, multi-dimensional acceleration measurement, speed/acceleration/shock measurement, etc., can solve problems such as high space requirements, and achieve the effect of suppressing zero-point deviation and compact structure
- Summary
- Abstract
- Description
- Claims
- Application Information
AI Technical Summary
Problems solved by technology
Method used
Image
Examples
Embodiment Construction
[0016] figure 1 A schematic diagram of a first embodiment of an acceleration sensor 300 is shown, which is arranged on the z-axis above the surface of a substrate 322 lying in the x-y plane. The acceleration sensor 300 is suitable for detecting accelerations in all three spatial directions x, y, z. Acceleration sensor 300 is made of, for example, a silicon substrate as a micromechanical component.
[0017] The acceleration sensor 300 includes an outer frame 313 arranged in an x-y plane. The outer frame 313 has a rectangular basic shape. The outer edge of the outer frame 313 is composed of a first frame part 316 , a second frame part 317 , a third frame part 318 and a fourth frame part 319 . The first frame member 316 and the third frame member 318 are oriented parallel to the y-axis. The second frame part 317 and the fourth frame part 319 are oriented parallel to the x-axis. The area enclosed by the first frame member 316, the second frame member 317, the third frame memb...
PUM
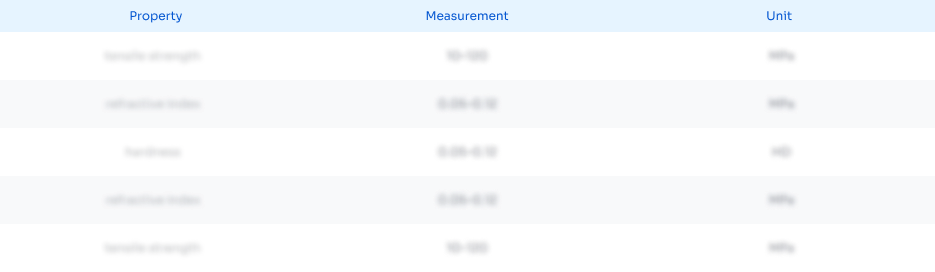
Abstract
Description
Claims
Application Information

- R&D
- Intellectual Property
- Life Sciences
- Materials
- Tech Scout
- Unparalleled Data Quality
- Higher Quality Content
- 60% Fewer Hallucinations
Browse by: Latest US Patents, China's latest patents, Technical Efficacy Thesaurus, Application Domain, Technology Topic, Popular Technical Reports.
© 2025 PatSnap. All rights reserved.Legal|Privacy policy|Modern Slavery Act Transparency Statement|Sitemap|About US| Contact US: help@patsnap.com