Joint of hyper-redundant robot
A robot joint and redundancy technology, applied in the field of robotics, can solve problems such as difficult control, difficult manufacturing, and complex structure, and achieve the effect of large driving torque, simple and compact structure, and smooth movement
- Summary
- Abstract
- Description
- Claims
- Application Information
AI Technical Summary
Problems solved by technology
Method used
Image
Examples
Embodiment Construction
[0013] The structure of the present invention will be described in further detail below in conjunction with the accompanying drawings.
[0014] combine figure 1 , figure 2 It can be seen that the joint bracket of the super-redundant robot has the following combination of gear transmission pairs: a cross-shaft gear 1 is mutually orthogonal to the axles 2 and 3, and then respectively communicates with the tongues 4 and 5 of the two joint brackets. coupling. The second pinion 6 and 7 are placed on two joint supports and meshed with two semicircular teeth of the cross shaft gear 1 . The two pinions are provided with drive motors 8 and 9. When the motor 8 drives the pinion 6 to rotate, and then drives the cross-shaft gear 1 and the bracket 10 to rotate, the joint produces side swing motion; when the motor 9 drives the pinion 7 to rotate, and then drives the cross-shaft gear 1 and the bracket 11 to rotate, the joint generates Pitching motion; when the two motors are driven simu...
PUM
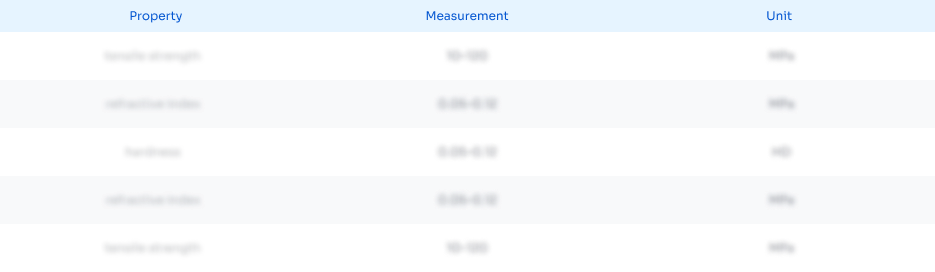
Abstract
Description
Claims
Application Information

- R&D
- Intellectual Property
- Life Sciences
- Materials
- Tech Scout
- Unparalleled Data Quality
- Higher Quality Content
- 60% Fewer Hallucinations
Browse by: Latest US Patents, China's latest patents, Technical Efficacy Thesaurus, Application Domain, Technology Topic, Popular Technical Reports.
© 2025 PatSnap. All rights reserved.Legal|Privacy policy|Modern Slavery Act Transparency Statement|Sitemap|About US| Contact US: help@patsnap.com