Flue gas afterheat recovery system
A recovery system, flue gas waste heat technology, applied in the direction of heat recovery system, heat recovery, preheating, etc., can solve the problems of energy waste, achieve the effect of effective utilization and saving of heat sources
- Summary
- Abstract
- Description
- Claims
- Application Information
AI Technical Summary
Problems solved by technology
Method used
Image
Examples
Embodiment Construction
[0013] The structure of the flue gas waste heat recovery system of the present invention will be described below with reference to the accompanying drawings.
[0014] Please refer to Fig. 1, the flue gas waste heat recovery system of the present invention mainly utilizes the waste heat of the flue gas at the tail of the boiler to heat the condensed water in the low-pressure regenerative heating system, so as to avoid energy waste caused by traditional low-pressure heaters due to steam extraction.
[0015] The flue gas waste heat recovery system includes a phase change heat exchanger 100 and an automatic control device 200 installed in the phase change heat exchanger 100 .
[0016] The phase change heat exchanger 100 adopts a split structure, which includes a phase change upper section 1 and a phase change lower section 9 . The phase change lower section 9 communicates with the phase change upper section 1 through the vapor riser 30 and the liquid downcomer 40 . The phase chan...
PUM
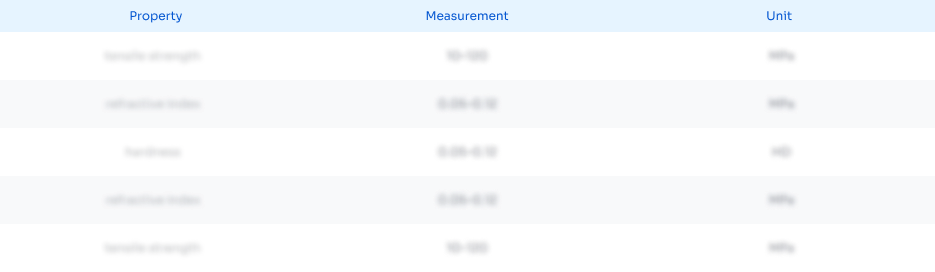
Abstract
Description
Claims
Application Information

- R&D Engineer
- R&D Manager
- IP Professional
- Industry Leading Data Capabilities
- Powerful AI technology
- Patent DNA Extraction
Browse by: Latest US Patents, China's latest patents, Technical Efficacy Thesaurus, Application Domain, Technology Topic, Popular Technical Reports.
© 2024 PatSnap. All rights reserved.Legal|Privacy policy|Modern Slavery Act Transparency Statement|Sitemap|About US| Contact US: help@patsnap.com