Method for controlling internal defects of steel
A technology for internal defects and steel, applied in the field of steel rolling, can solve problems such as increased deformation, and achieve the effects of reducing rolling passes, reducing production costs, and improving production costs and operational control difficulties.
- Summary
- Abstract
- Description
- Claims
- Application Information
AI Technical Summary
Problems solved by technology
Method used
Image
Examples
Embodiment 1
[0037] Adopt the following method to roll the 360×450mm continuous casting billet into 250×250mm axle steel: First, ensure sufficient soaking time during the heating process of the billet (here, the soaking time is determined according to the billet specification, in In this embodiment, a soaking time of ≥ 1.5 hours is adopted to make the temperature inside and outside the slab uniform; then, adjust the high-pressure water descaling parameters after being out of the furnace, so that the surface temperature of the slab is rapidly reduced, and the surface temperature of the slab is controlled. The temperature is lower by 100°C to 150°C; then, rolling is performed using the rolling process in Table 2 below.
[0038] In Example 1, the steps for adjusting the high-pressure water descaling parameters are as follows: increase the high-pressure water descaling equipment from 3.2m to 5m, use 12Mpa water pressure for the first 3m to ensure the descaling effect, and use 10Mpa water pressu...
Embodiment 2
[0046] Adopt the following method to roll the 360×450mm cast slab into 260×260mm square steel: first, ensure sufficient soaking time in the heating process of the cast slab (the soaking time is determined according to the cast slab specification, in this embodiment Adopted ≥ 1.5 hours of soaking time) to make the internal and external temperature of the slab uniform; then, adopt the same method as the method in embodiment 1 to adjust the high-pressure water descaling parameters after being out of the furnace, so that the surface temperature of the slab is rapidly reduced, and the control center The part is 100°C-150°C higher than the surface temperature; then, the rolling process in Table 3 is used for rolling. In Table 3, the reduction rate of the sixth pass is 25%, and the shape coefficient of the deformation zone is 0.64.
[0047] Table 3 Rolling process of 260×260mm square steel by the method of Example 2
[0048]
pass
Billet inlet specification
...
Embodiment 3
[0053] Adopt the following method to roll the slab of 360×450mm into square steel of 230×230mm: first, ensure sufficient soaking time in the heating process of the slab (the soaking time is determined according to the specification of the slab, in this embodiment Adopted ≥ 1.5 hours of soaking time) to make the internal and external temperature of the slab uniform; then, adopt the same method as the method in embodiment 1 to adjust the high-pressure water descaling parameters after being out of the furnace, so that the surface temperature of the slab is rapidly reduced, and the control center The part is 100°C-150°C higher than the surface temperature; then, the rolling process in Table 4 is used for rolling. In Table 4, the reduction rate of the sixth pass is 25.4%, and the shape coefficient of the deformation zone is 0.67; the reduction rate of the seventh pass is 25.0%, and the shape coefficient of the deformation zone is 0.66.
[0054] Table 4 Rolling process of 230×230mm ...
PUM
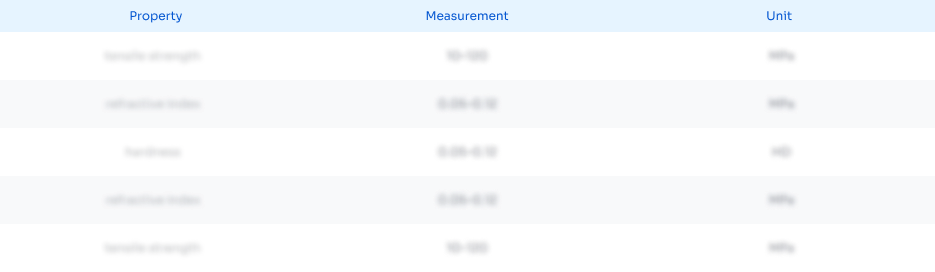
Abstract
Description
Claims
Application Information

- R&D
- Intellectual Property
- Life Sciences
- Materials
- Tech Scout
- Unparalleled Data Quality
- Higher Quality Content
- 60% Fewer Hallucinations
Browse by: Latest US Patents, China's latest patents, Technical Efficacy Thesaurus, Application Domain, Technology Topic, Popular Technical Reports.
© 2025 PatSnap. All rights reserved.Legal|Privacy policy|Modern Slavery Act Transparency Statement|Sitemap|About US| Contact US: help@patsnap.com